Steel Glossary
TENASTEEL
C | S max | Mn | Cr | Mo | V | Others |
---|---|---|---|---|---|---|
1.00 | 0.005 | 0.35 | 7.50 | 2.60 | 0.30 | Ti |
TENASTEEL is a cold work steel that combines high compressive strength with outstanding toughness. It is known for its high hot strength and good machinability in the as-delivered condition, with a maximum hardness of 250 HB.
It has been specifically designed to replace the commonly used 1.2379 / X 153 CrMoV 12 steel, which is sometimes prone to fractures. TENASTEEL solves many tool life problems, especially related to cutting edge chipping or cracking in 1.2379. Thanks to its alloy composition and suitable heat treatment, TENASTEEL is particularly suitable for surface coatings.
TENASTEEL is a trademark product of the French manufacturer Industeel, exclusively distributed in Germany by Gebrüder Recknagel.
Mechanical Properties
(Typical values)Hardness [HB] in annealed condition | Hardness [HRC] treated condition | Elastic modulus [MPa] | Compressive strength [MPa] | Charpy impact toughness [J/cm2] (*) |
---|---|---|---|---|
250 HB max | 56 | 205 | 2210 | 40 |
62 | 205 | 2550 | 25 |
Physical Properties
Thermal Conductivity at 20 °C [W·m-1·K-1] |
Average Coefficients of Thermal Expansion [10-6 K-1] |
|||
---|---|---|---|---|
20 – 100°C | 20 – 1,200°C | 20 – 1,300°C | 20 – 1,400°C | |
21 | 10.2 | 11.3 | 11.9 | 12.8 |
Specific Heat Capacity (20°C) [J·kg-1·K-1] |
Density (20°C) [kg·dm-3] |
---|---|
460 | 7.75 |
Wear Resistance
The wear resistance of TENASTEEL is close to that of steel 1.2379 / X 153 CrMoV 12, with lower levels of carbon and chromium compensated by the addition of alloying elements that form finer and harder carbides than chromium carbides.
Note: The wear resistance is considered only for uncoated tools. If a coating (PVD/CVD) is present, which counteracts wear, the toughness and compressive strength of the base material are taken into account.
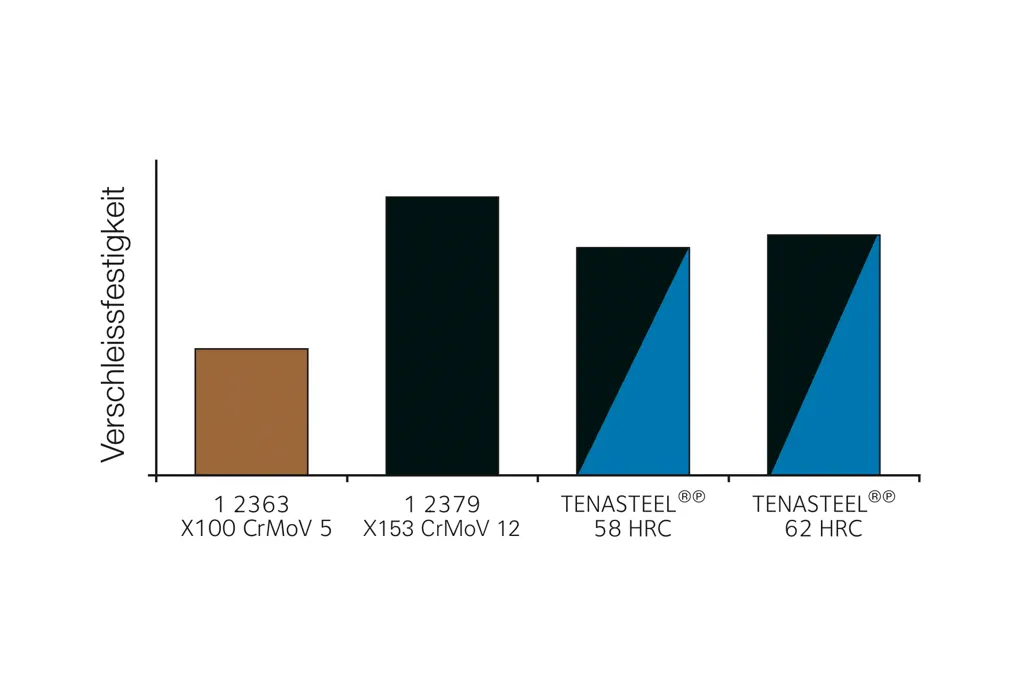
Compressive Strength
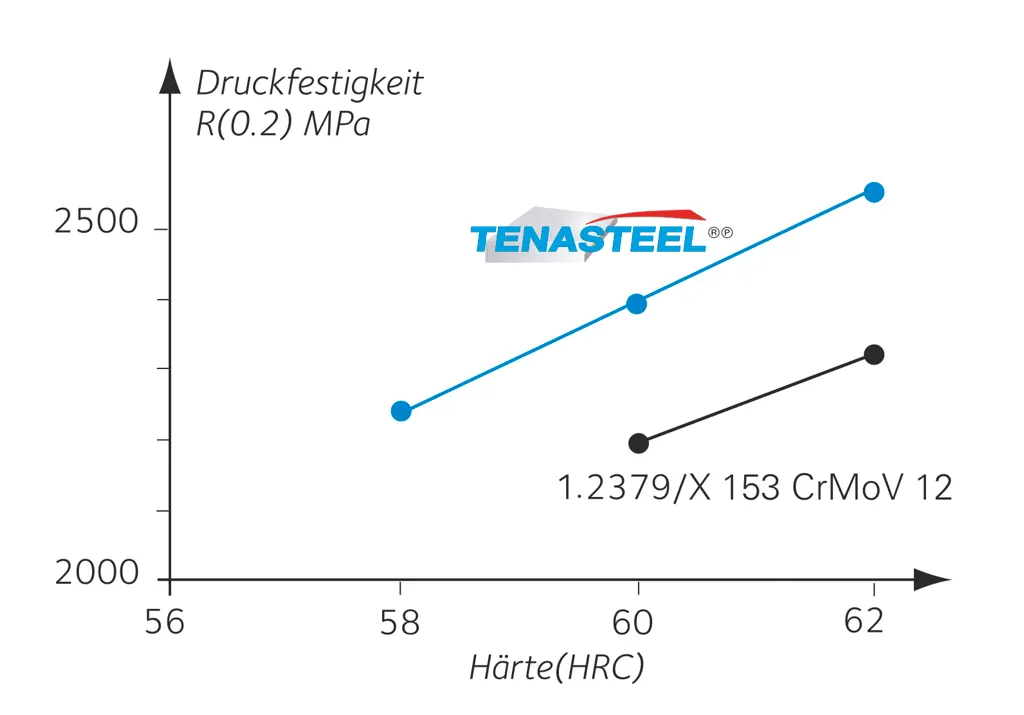
Metallurgical Properties
Inclusion CleanlinessThe inclusion cleanliness of TENASTEEL is guaranteed according to NFA 04-106 Method A.
Value | A | B | C | D |
---|---|---|---|---|
Index | ≤ 1.5 | ≤ 1.5 | ≤ 1 | ≤ 1.5 |
Microstructure
In the as-delivered state, TENASTEEL's microstructure consists of a ferritic matrix. Small primary carbides that form from the solidification of the alloy, as well as very fine secondary carbides resulting from annealing, are homogeneously distributed in this matrix.
The microphotographs depicted below perfectly illustrate the general refinement achieved with TENASTEEL's structure compared to 1.2379 / X 153 CrMoV 12.
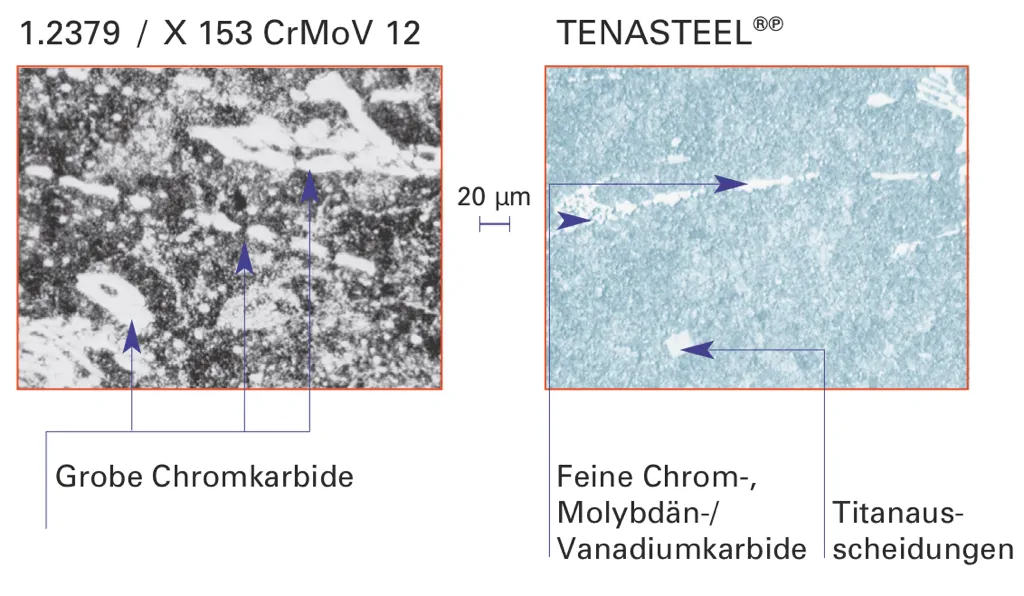
This difference in microstructure results in a significant improvement in toughness and machinability, while the wear resistance is maintained at a good level thanks to the presence of carbides that are harder than those typically found in 1.2379 / X 153 CrMoV 12.
Transformation Points
Test conditions: Heating at a rate of 150°C/hour up to 1,000°C and rapid cooling.
AC1°C | ACm°C | Ms°C |
---|---|---|
845 | 880 | 200 |
Continuous Cooling Transformation Diagram
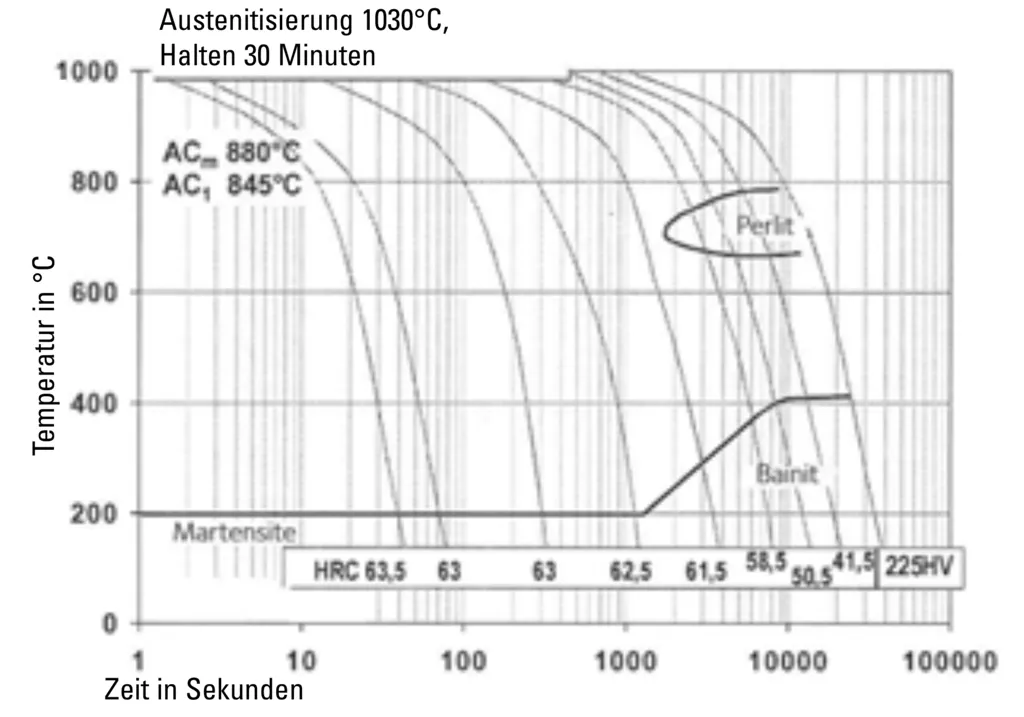
Isothermal Time Temperature Transformation Diagram
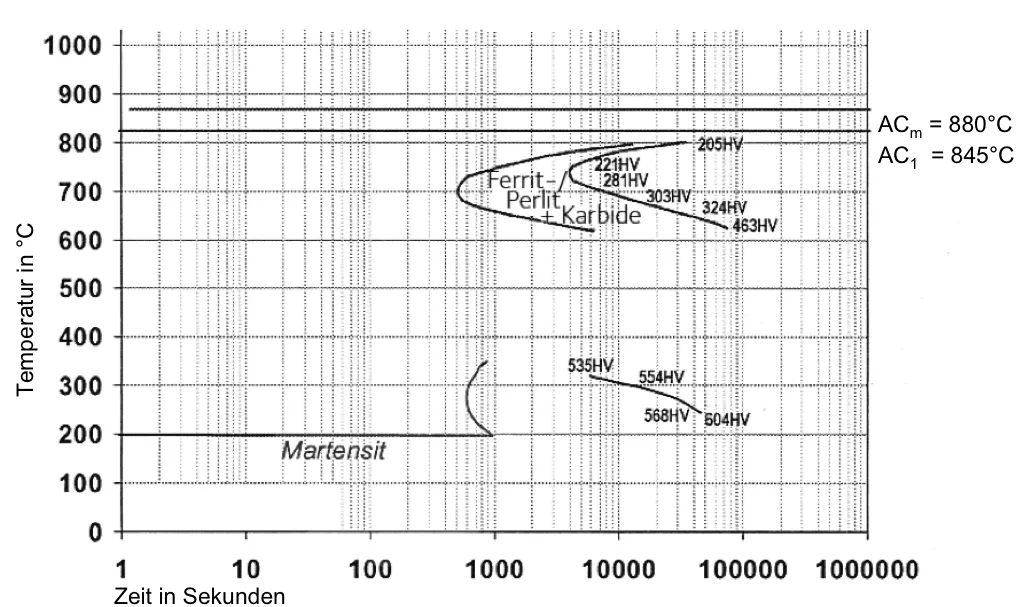
Heat Treatment
Austenitization
Heating at a moderate rate up to 750°C and holding. Slowly heat up to 1,030/1,050°C, hold for ½ hour per 25 mm.
Note: The heating cycle must be done under vacuum or protective gas to prevent oxidation and decarburization of the surface.
Quenching
After austenitization, preferentially cool under gas pressure; otherwise, use salt bath or fluidized bed cooling at temperatures between 250 and 350°C.
Oil quenching should be reserved for tools with simple geometry if other mentioned methods do not provide sufficient cooling rates (see Time-Temperature-Transformation diagrams).
Tempering must be carried out as soon as the tool temperature reaches 40 to 60°C, except in the case of deep cryogenic treatment (see "Deep Cryogenic Treatment" section).
Tempering
Depending on the application, the desired final hardness is achieved by adjusting the tempering temperatures, which are carried out using the tempering curves shown below for the target hardness.
After the initial tempering, a nearly identical second tempering is performed at a slightly lower temperature to achieve a fully tempered final structure and ensure dimensional stability of the treated part.
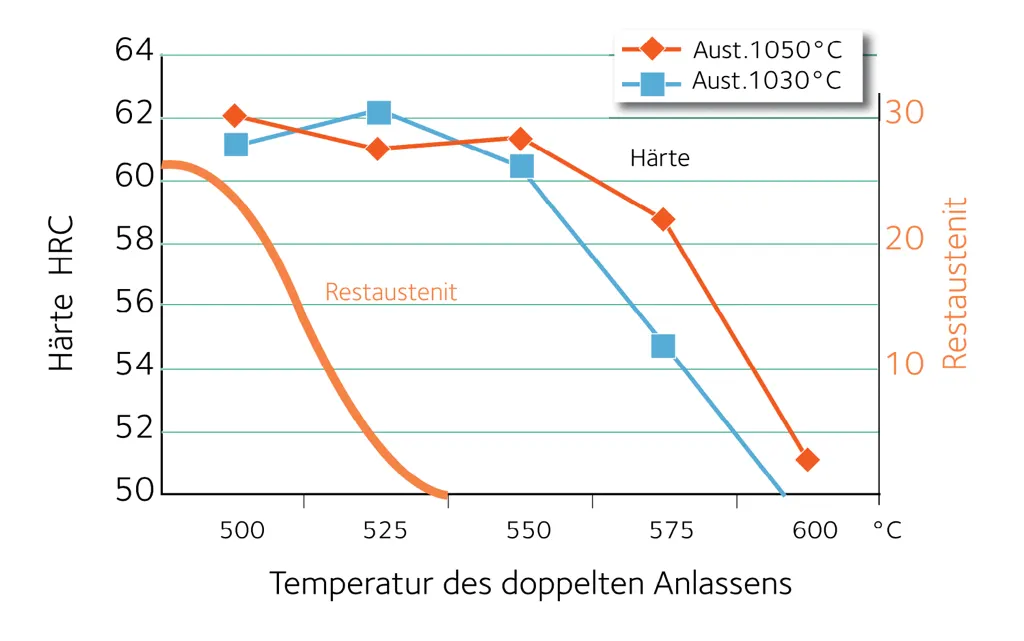
The chart shows that high austenitization temperature (1,050°C) leads to a hardness of 58 HRC even after tempering at 575°C.
TENASTEEL allows for high tempering temperatures. After tempering at high temperature (e.g., 550°C), the content of retained austenite is very low, and the treated parts exhibit excellent dimensional stability during use.
Conversely, parts tempered at temperatures below 500°C (20% retained austenite) may experience dimensional changes after treatment.
The desired hardness level in heat treatment significantly affects toughness. Depending on the operating conditions (pressure, shocks, mechanical properties of the deformed steel), as well as the intended surface treatment and coating of the tool, it is possible to adjust the best compromise between wear resistance and toughness using hardness and tempering temperature.
The following diagram can assist in the selection process. In any case, TENASTEEL provides a better hardness/toughness compromise compared to 1.2379 / X 153 CrMoV 12.
If you have any doubts, please don't hesitate to contact us. We are happy to assist you with our advice.
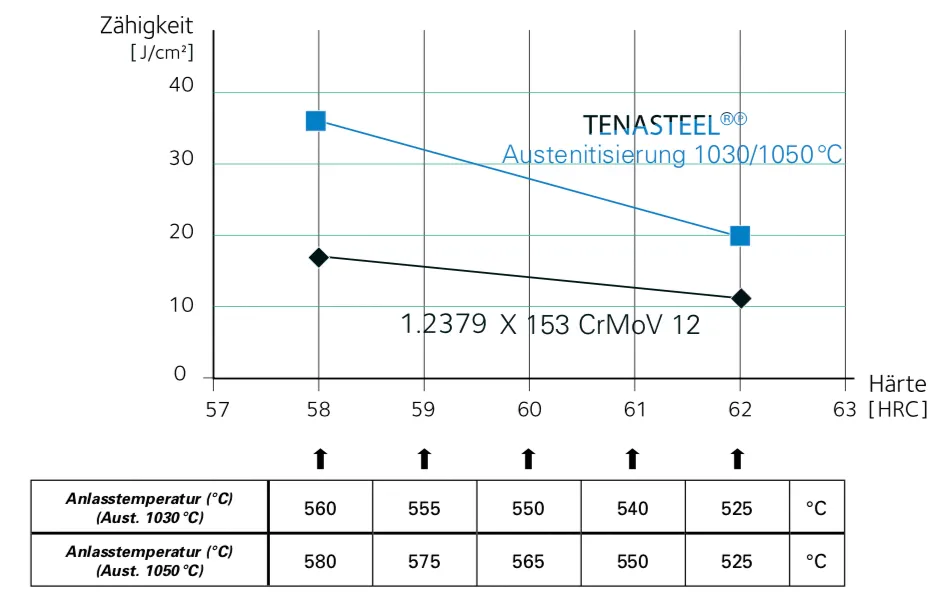
Cryogenic Treatment
The remaining retained austenite in the steel after hardening is effectively reduced to almost zero through cryogenic treatment. This prevents dimensional changes due to later retained austenite transformations. If necessary, cryogenic treatment can be performed as follows:
Cryogenic Treatment Cycle
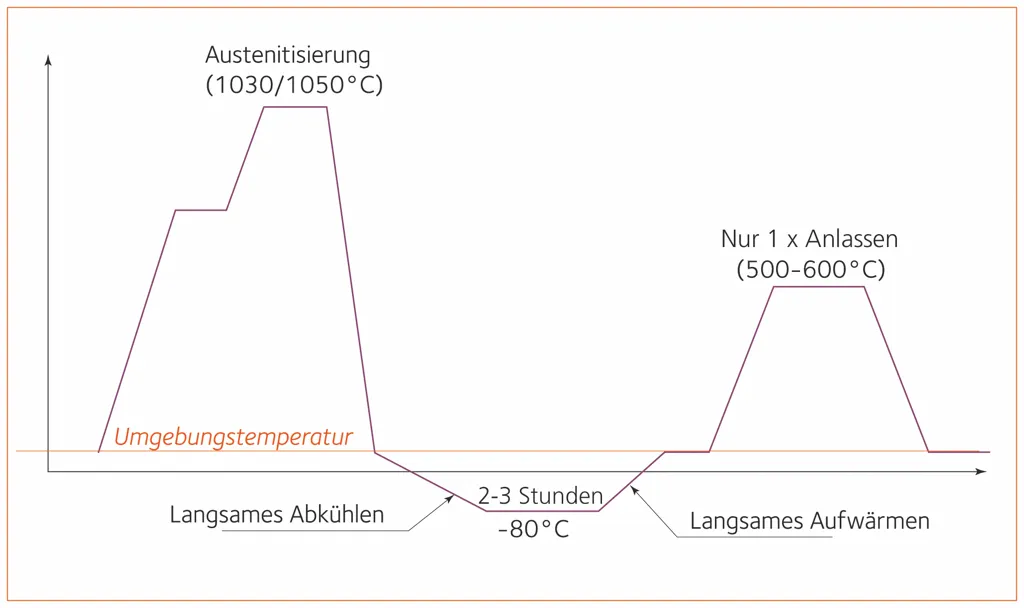
Tempering Curve after Cryogenic Treatment
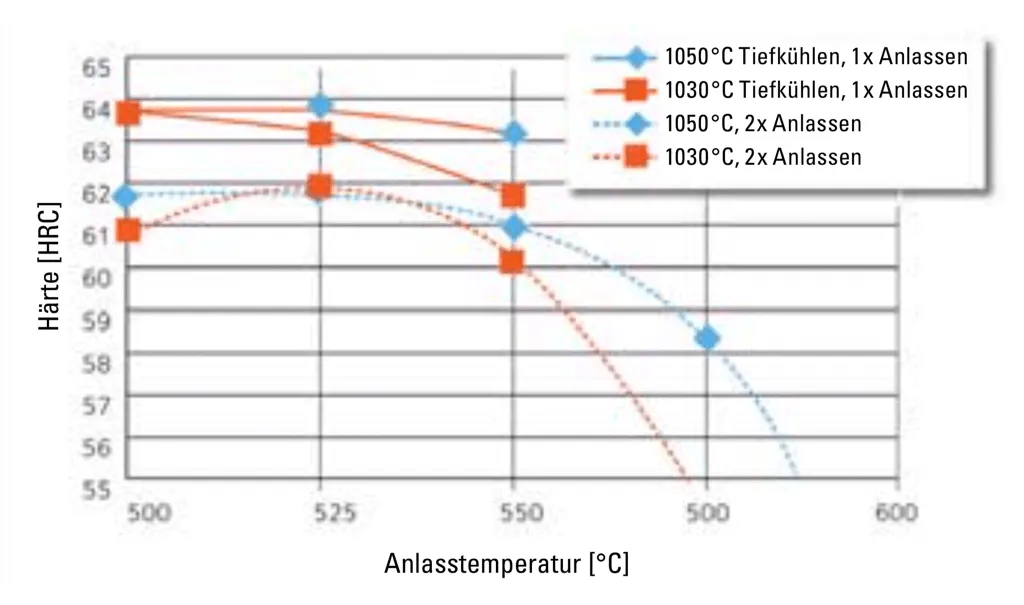
Surface Coatings
Coatings on the tools, like surface hardening, offer high wear resistance and a significant reduction in friction coefficients.
These processes differ from the previous ones in that an exogenous material layer is applied, which does not react with the base material and acts as an additional "skin."
PVD: Physical Vapor Deposition
These types of depositions can be performed at relatively low temperatures (200 to 500 C) and do not affect the hardness of the base material. The achieved hardness can reach 2,000 HV on a few micrometers.
Please note that for post-hardening PVD coating, the material must be tempered at temperatures above 500°C.
CVD: Chemical Vapor Deposition
The temperature required to activate the reactions for CVD treatment is so high (800 to 1,000°C) that a new heat treatment is necessary to adjust the hardness of the part after coating. The hardness of the coatings can reach and even exceed 2,500 HV.
Nitriding
Nitriding treatment aims to increase surface hardness and wear resistance while reducing friction coefficients by enriching one or more elements in the surface layer of the part.
TENASTEEL is well-suited for nitriding due to its high hardness and excellent tempering resistance.
Conventional gas and plasma nitriding at temperatures around 500°C to 525°C allows the achievement of a hard layer of over 1,100 HV with a thickness of several micrometers.
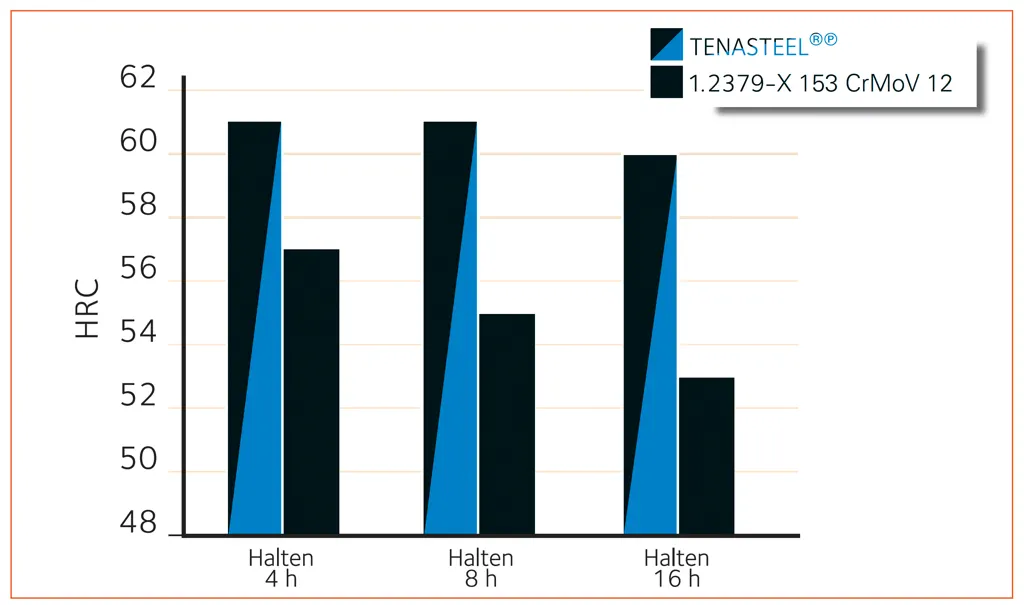
Please note that for post-hardening nitriding treatment, the material must be tempered at a minimum of 525°C.
In the depicted chart, it can be observed that the core hardness of TENASTEEL is not affected by the nitriding treatment, while 1.2379 / X 153 CrMoV 12 experiences a hardness drop of 5 to 10 HRC under the nitrided layer.
Hardness variation for 16-hour gas nitriding
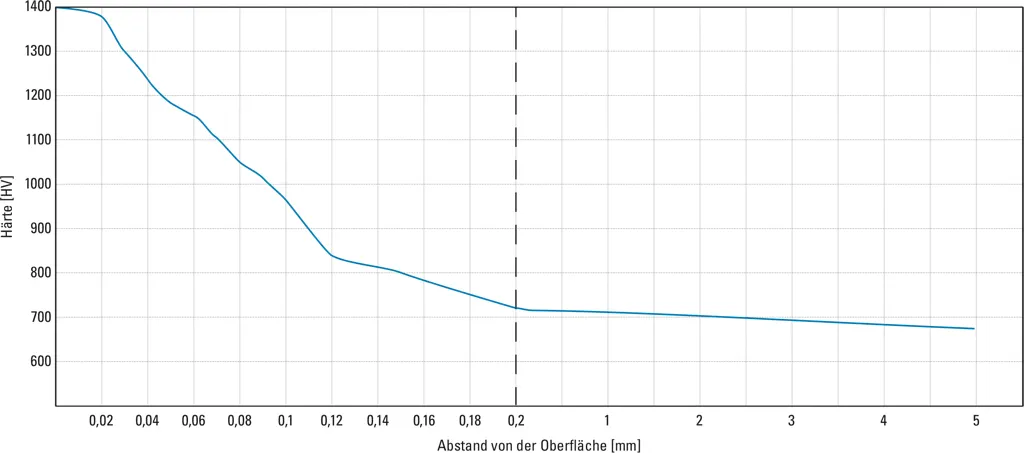
Machining - In Annealed Condition
Cutting Parameters | Roughing | Finishing |
---|---|---|
Cutting Speed (vc) – m/min | 130 - 190 | 170 - 210 |
Feed Rate (Fz) – mm/tooth | 0.15 - 0.4 | 0.1 - 0.2 |
Cutting Depth (ap) – mm | 2 - 5 | ≤ 1.5 |
Cutting Parameters | ∅ ≤ 10 | ∅ 10 - 20 |
---|---|---|
Cutting Speed (vc) – m/min | 15 | 15 |
Feed Rate (Fz) – mm/rev | 0.05 - 0.2 | 0.2 - 0.3 |
EDM - Electro-Discharge Machining
TENASTEEL is suitable for all EDM processes before and after heat treatment.
If EDM is performed in the hardened condition, the part should be immediately finished, and the EDM surfaces should be polished or stress-relief annealed (20 °C below the last tempering temperature).
Welding
The repair or build-up welding of tools made from TENASTEEL can be considered with the use of appropriate filler materials while adhering to essential precautions. For further information, we are happy to provide you with the TENASTEEL Handbook.
Applications
TENASTEEL is an advantageous replacement for the standardized steel 1.2379 / X 153 CrMoV 12 in all its applications, including cutting tools, extrusion dies, forming tools, embossing tools, machine knives, etc.
Attention please!
Some features of our webshop are not supported by your current browser version.
We recommend updating your browser or using a different browser.