Steel Glossary
Daido DRM1
C | Si | Mn | Cr | Mo | W | V | Co | |
---|---|---|---|---|---|---|---|---|
Typical Composition (Weight %) | 0.5 | 0.2 | 0.5 | 4.2 | 1.0 | 3.0 | 1.3 | 2.0 |
Treatment Temperatures | Hardness | ||||
---|---|---|---|---|---|
Hot Forming | Annealing | Hardening | Tempering | Soft Annealing | Hardened |
(please inquire) | 800 - 880°C Slow cooling |
1,100 - 1,140°C Quenching in oil, gas, or salt bath |
550 - 620°C Minimum 2x tempering, air-cooling |
≤ 235 HB | 56 – 58 HRC |
Physical Properties | ||||||||
---|---|---|---|---|---|---|---|---|
Coefficient of thermal expansion [10-6/K] | 20 - 100°C | 20 - 200°C | 20 - 300°C | 20 - 400°C | 20 - 500°C | 20 - 600°C | 20 - 700°C | 20 - 800°C |
11.2 | 11.4 | 11.7 | 11.9 | 12.2 | 12.4 | 12.7 | 12.3 | |
Thermal Conductivity [W/mK] | 25°C | 200°C | 300°C | 400°C | 500°C | 600°C | 700°C | |
22.4 | 26.3 | 27.3 | 28.6 | 28.4 | 29.1 | 28.8 | ||
Specific Heat [J/kgK] | 25°C | 200°C | 300°C | 400°C | 500°C | 600°C | 700°C | |
413 | 487 | 519 | 562 | 616 | 705 | 840 |
E-Modul = 210 GPa, The Sample Was Hardened At 1,140°C And Tempered Twice At 560°C
Microstructure
DRM1
(In The Center Of The Bar, Diameter 100 mm)
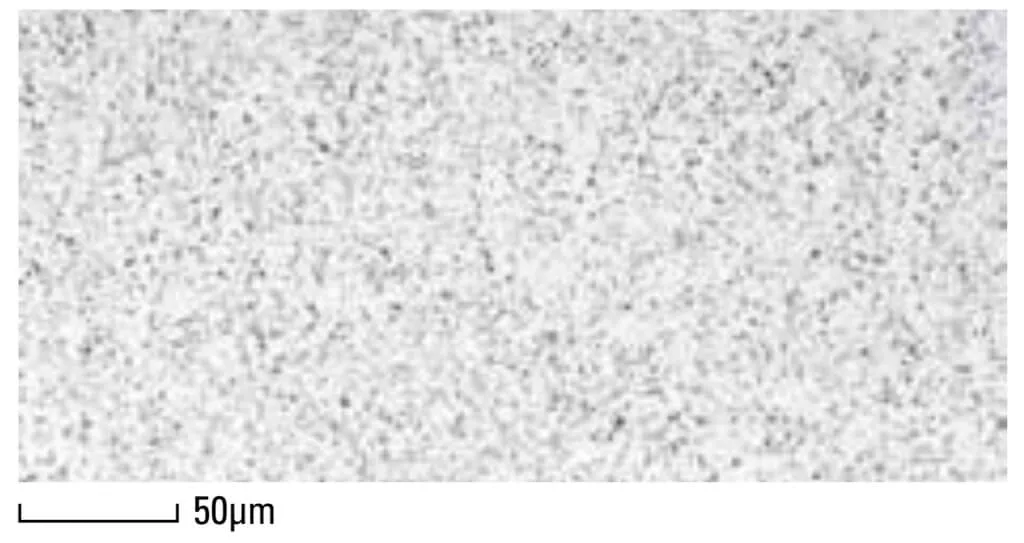
Conventional Hot Work Steel
(Daido)
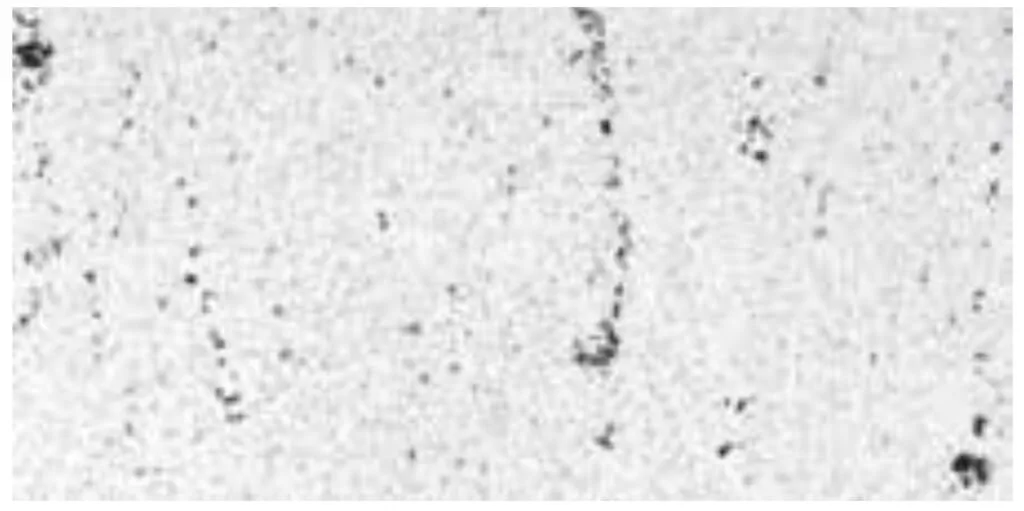
Tempering Treatment
Sample: Square 15 mm, quenched in oil, tempered with air cooling
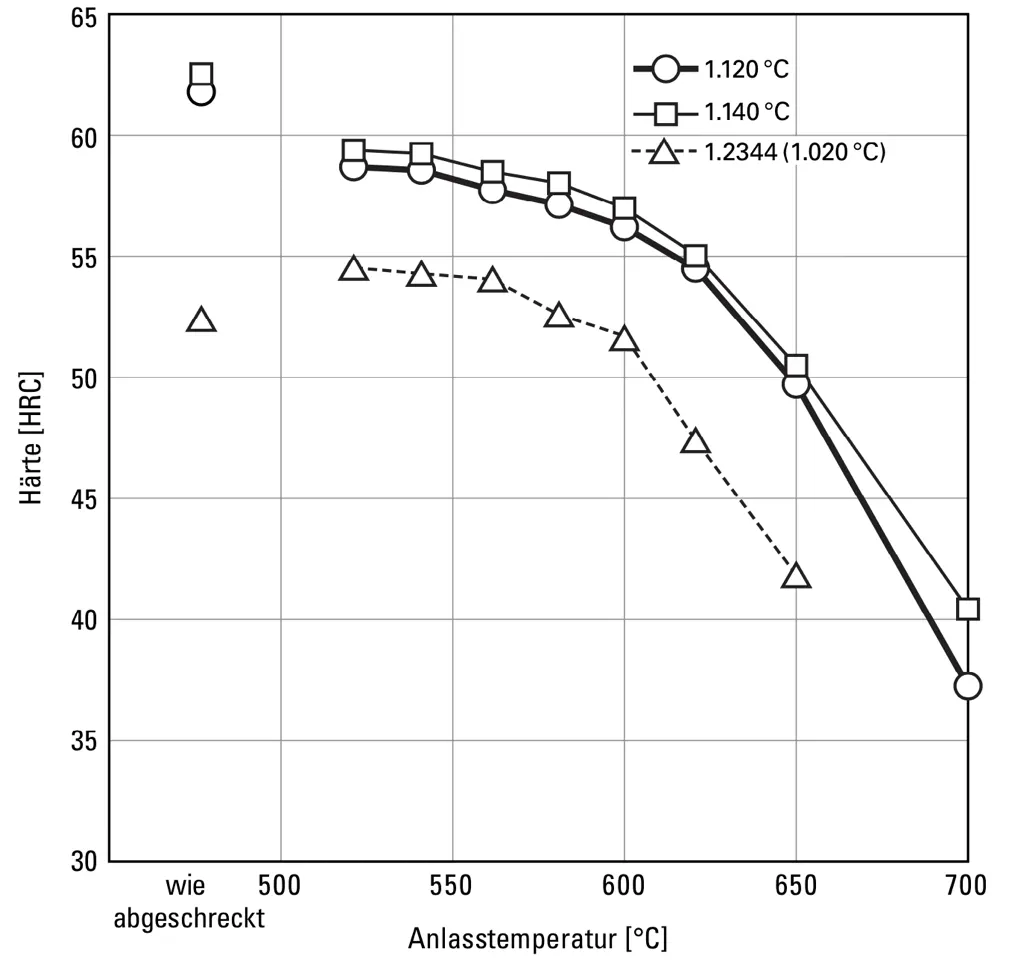
Charpy Impact Toughness
Samples: taken from round bar, in the center of the diameter 100 mm, notched U-shaped specimen
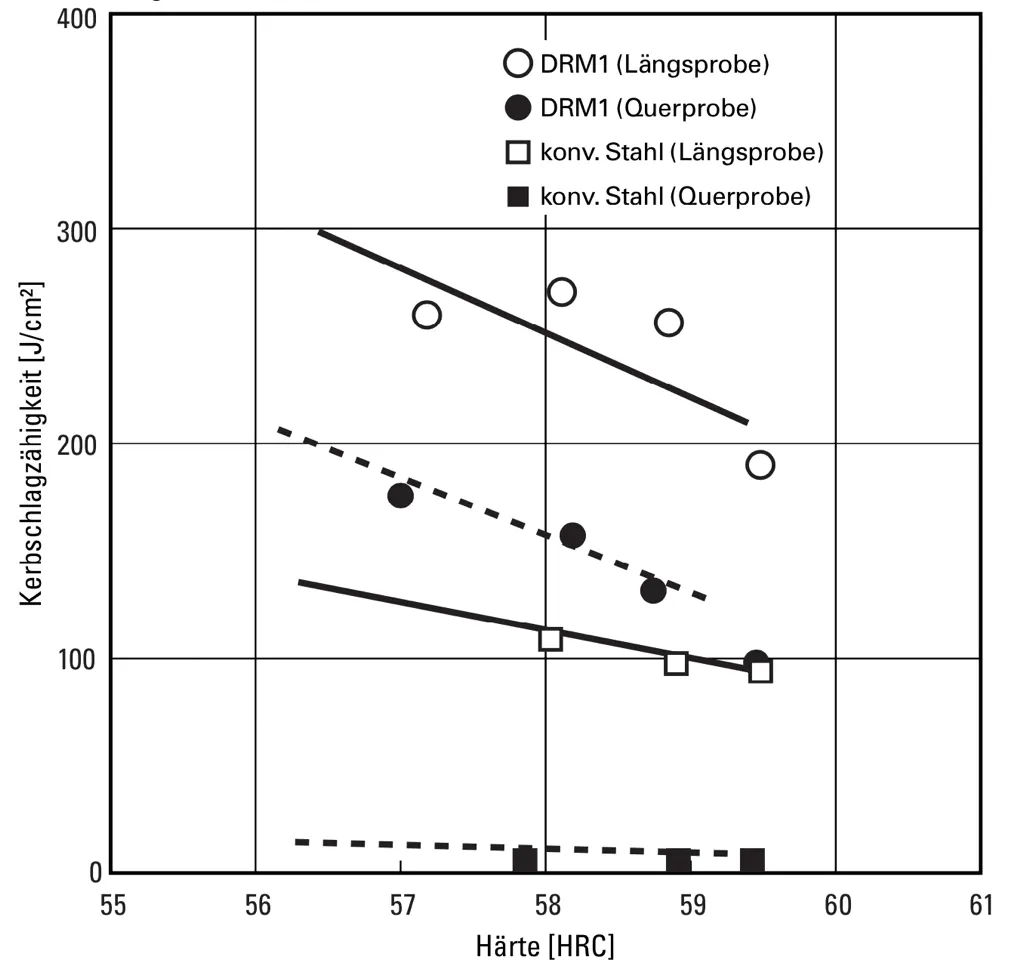
Heat Treatment | ||
---|---|---|
Hardening | Tempering | |
DRM1 | 1,140°C, oil quenched | 540 - 600°C, double tempered |
Conventional Steel | 1,120°C, oil quenched | 540 - 600°C, double tempered |
Time-dependent tempering resistance
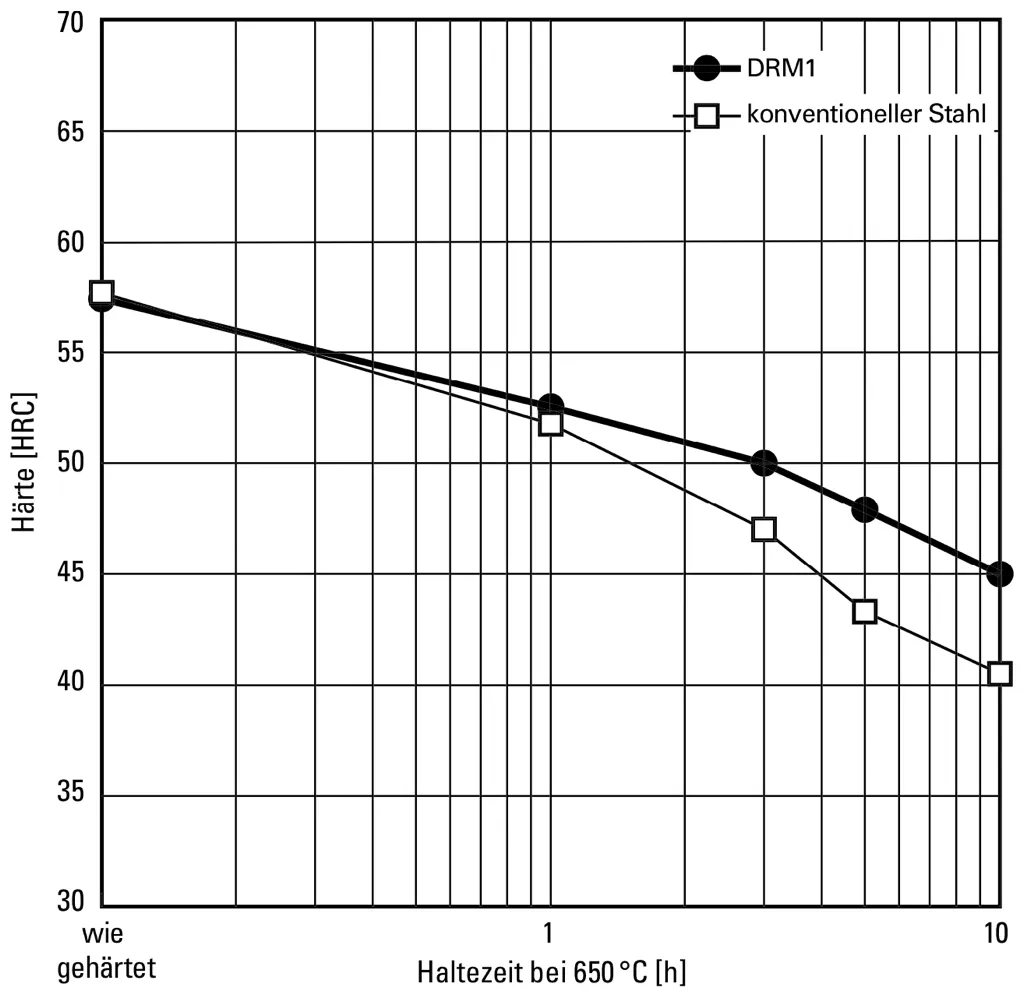
Heat Treatment | ||
---|---|---|
Hardening | Tempering | |
DRM1 | 1,140°C, oil quenched | 600°C, double tempered |
Conventional Steel | 1,120°C, oil quenched | 610°C, double tempered |
Hardness at Elevated Temperatures
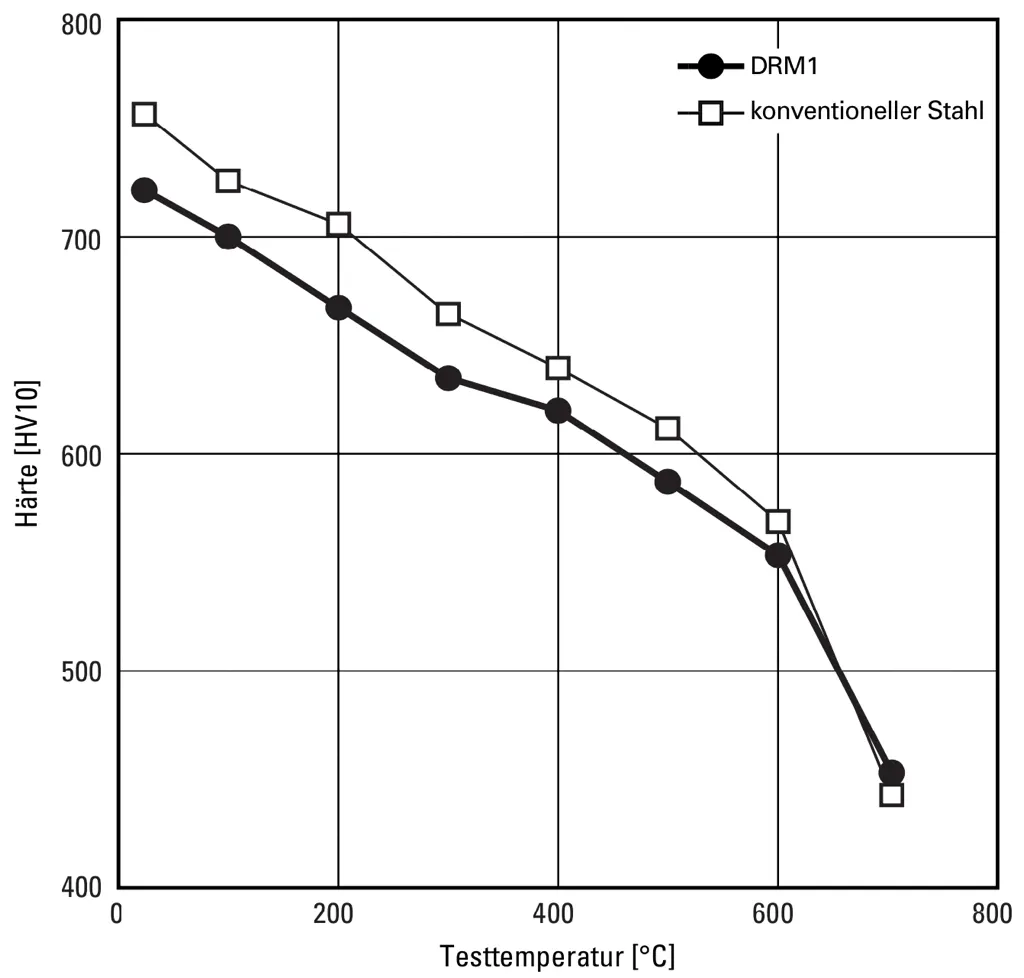
Heat Treatment | ||
---|---|---|
Hardening | Tempering | |
DRM1 | 1,140°C, oil quenched | 560°C, double tempered |
Conventional Steel | 1,140°C, oil quenched | 560°C, double tempered |
Fire Crack Resistance
Sample: ∅ 15 mm, 10 mm thick
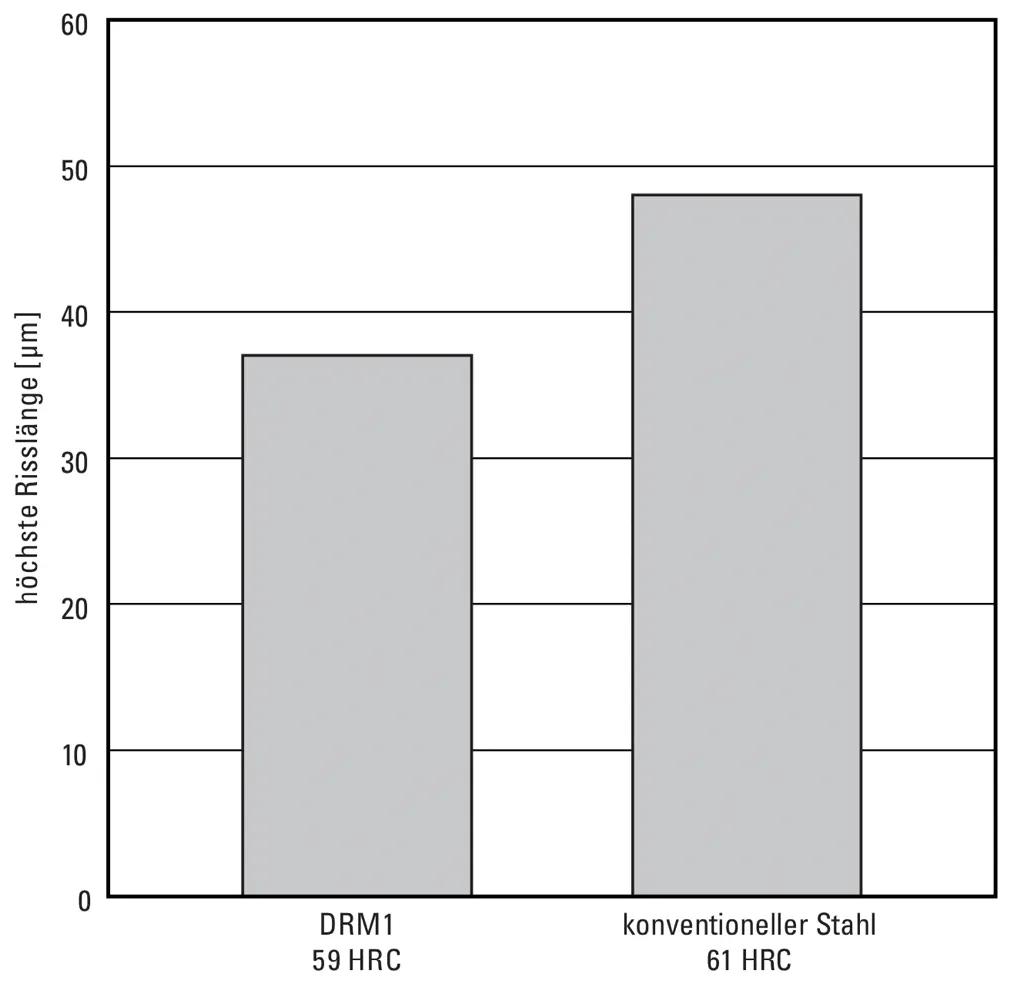
Heat Treatment | ||
---|---|---|
Hardening | Tempering | |
DRM1 | 1,140°C, oil quenched | 560°C, double tempered |
Conventional Steel | 1,140°C, oil quenched | 560°C, double tempered |
Test Method | Induction heating to 700°C, cooling to 20°C, repeated 1,000 times |
Endurance Strength / Material Fatigue
Samples: taken from the center of a bar ∅ 100 mm
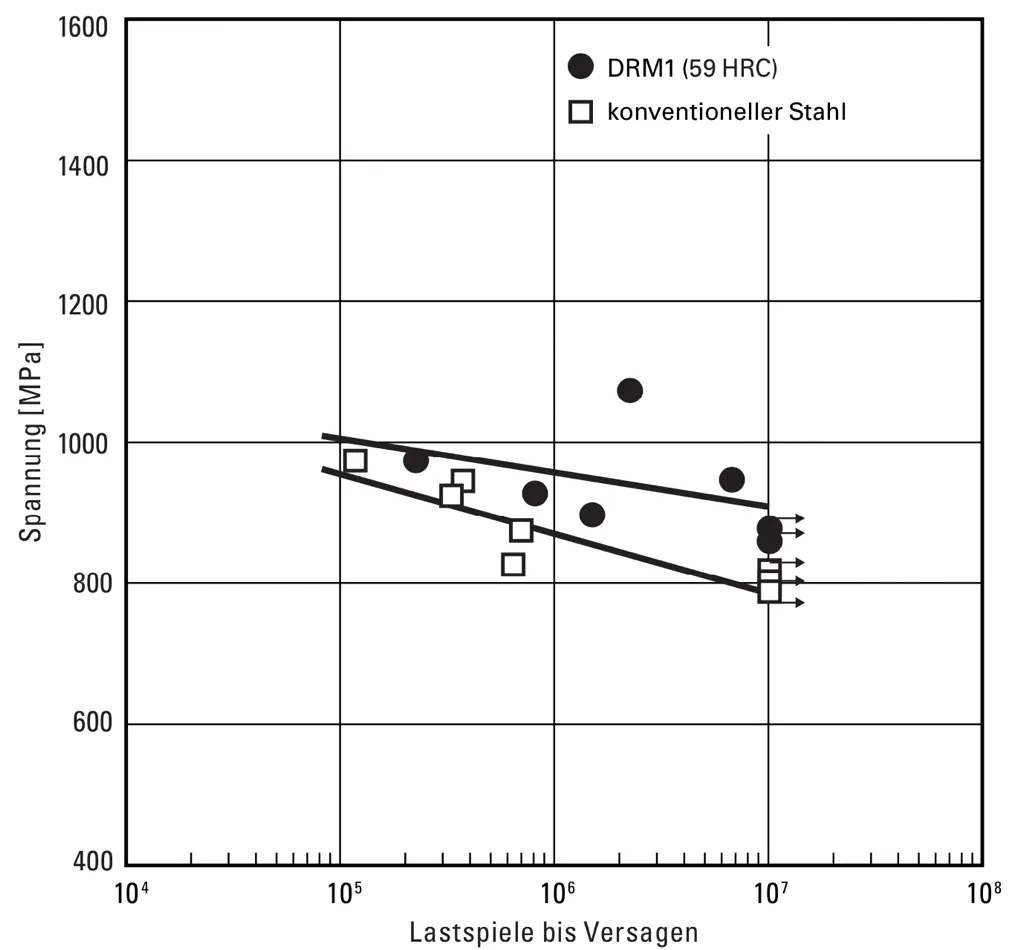
Heat Treatment | ||
---|---|---|
Hardening | Tempering | |
DRM1 | 1,140°C, oil quenched | 560°C, double tempered |
Konventional Steel | 1,140°C, oil quenched | 560°C, double tempered |
Test Method | Wöhler bending Test at room temperature |
Hardenability
Sample: Round steel ∅ 100 mm
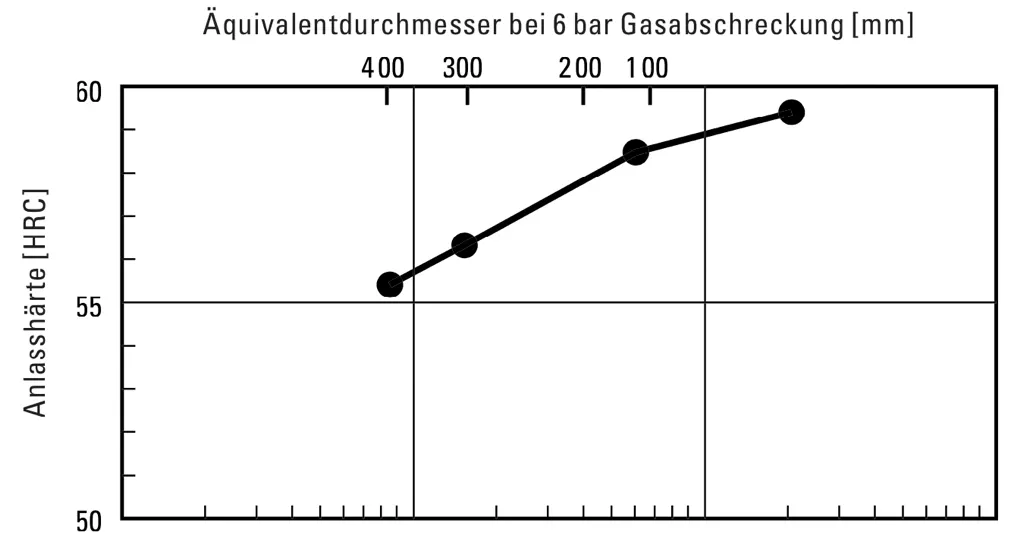
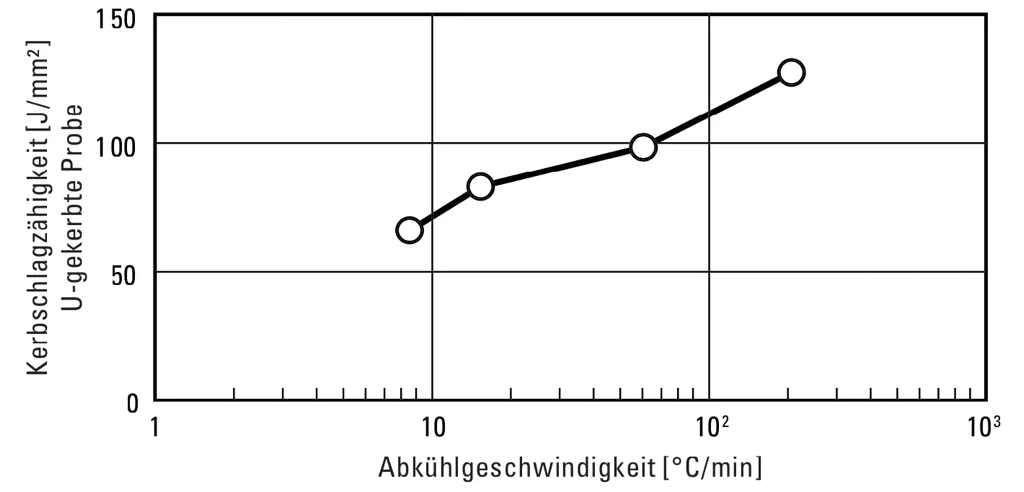
Wärmebehandlung | ||
---|---|---|
Härten | Anlassen | |
DRM1 | 1,140°C, 200°C/min entsprechend Ölhärtung | 560°C, zweifach angelassen |
Dimensional Changes During Hardening
Specimens: Rod steel ∅ 100 mm x 60 mm length
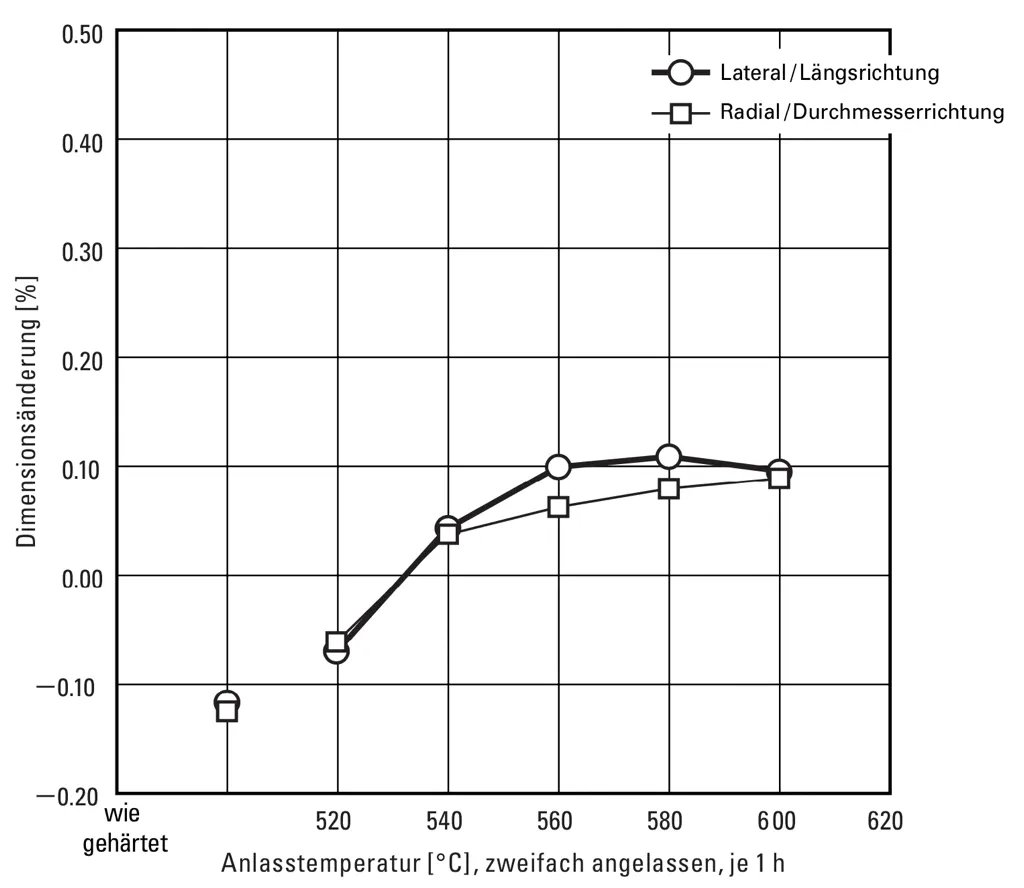
Heat Treatment | |
---|---|
Hardening | |
DRM1 | 1,140°C, oil quenched |
Hardness processes
Salt bath
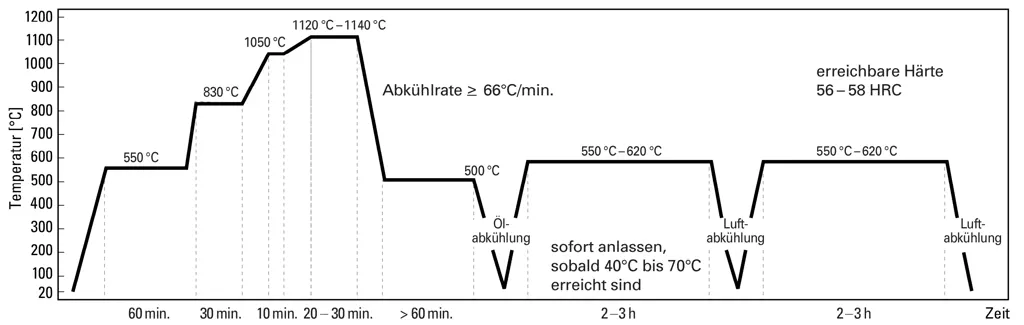
Vacuum
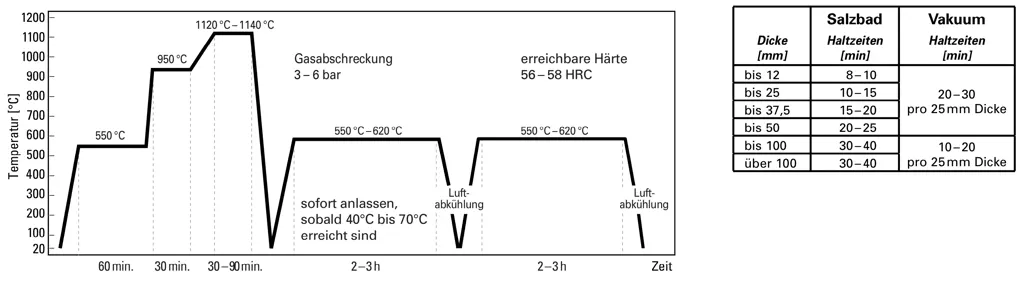
Nitriding
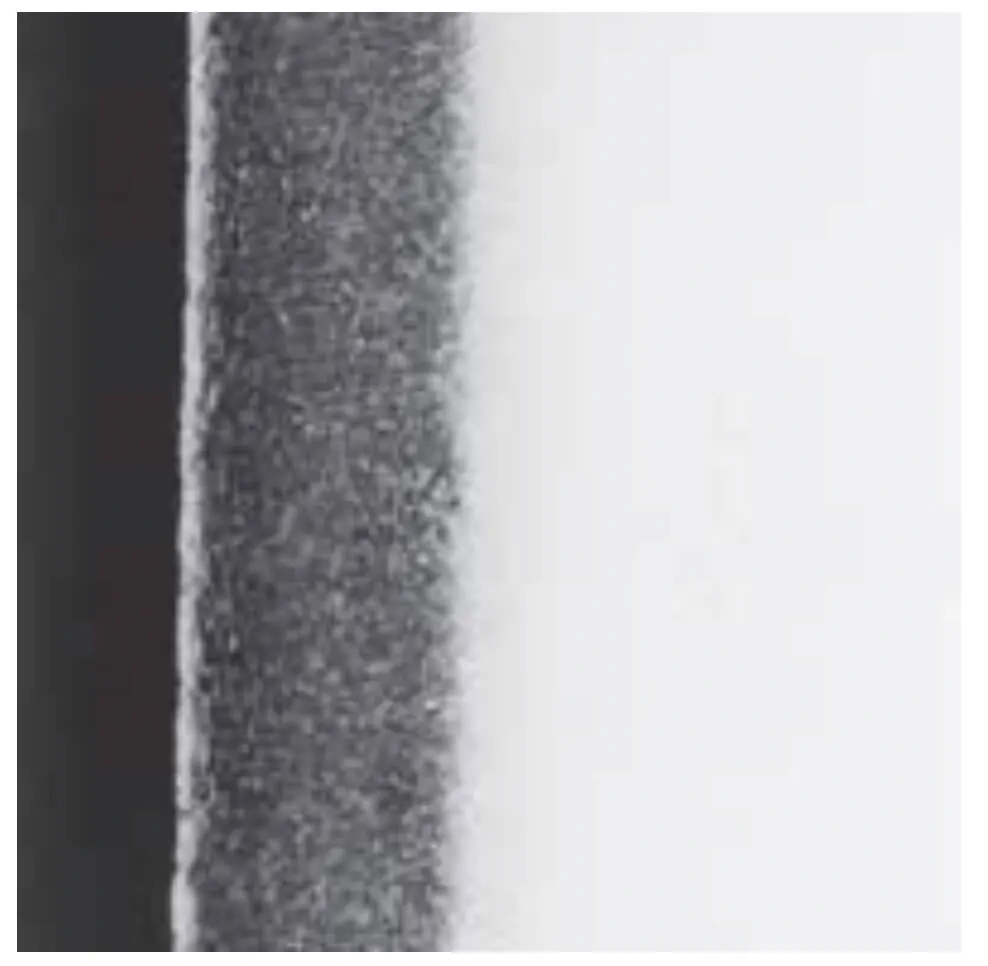
Example of the microstructure of a nitrided surface using Daido Amistar's PS process.
Hardness profile after nitriding.
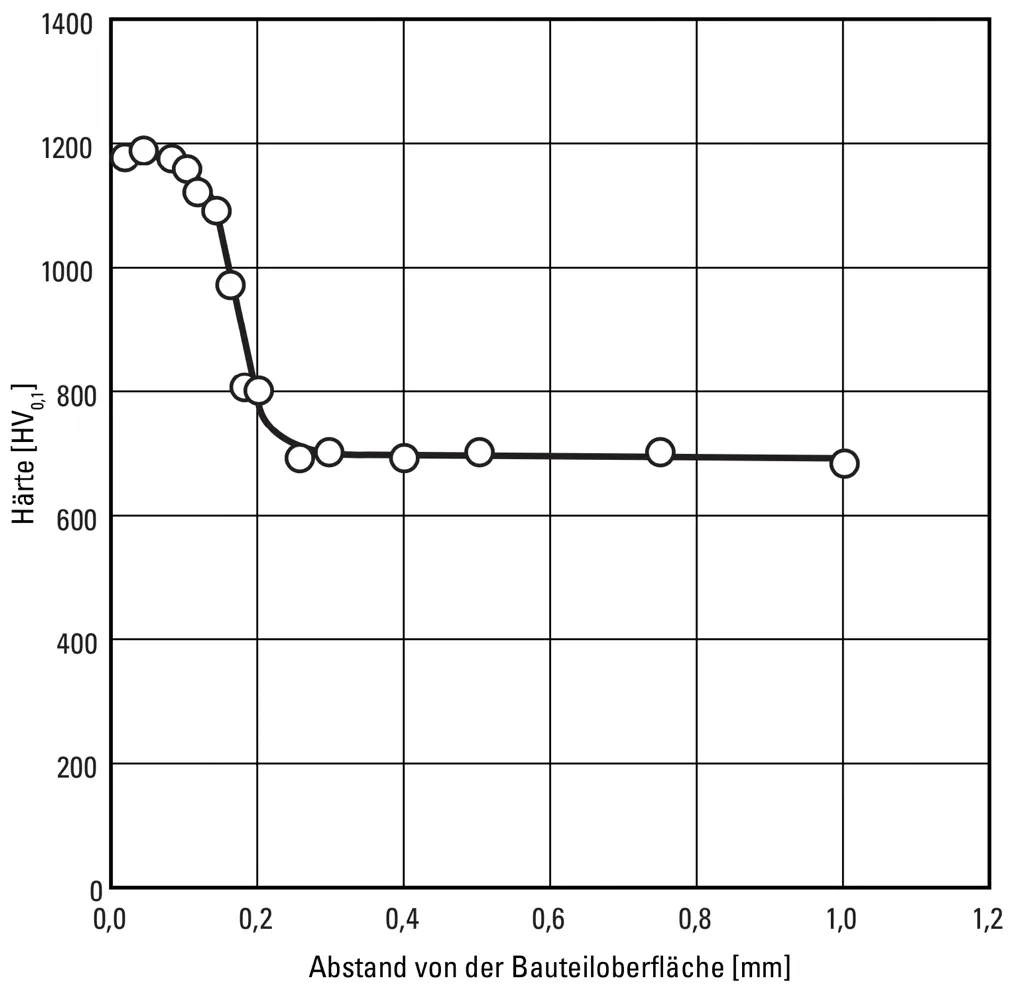
The surface hardness reaches 1,200 HV with NHD = 0.2 mm.
Representative technical values are provided based on our investigations. Unless otherwise stated, they do not constitute guarantees. Please seek individual advice for specific cases.
Attention please!
Some features of our webshop are not supported by your current browser version.
We recommend updating your browser or using a different browser.