Steel Glossary
Hardox 400
C | Si | Mn | P | S | Cr | Ni | Mo | B | |
---|---|---|---|---|---|---|---|---|---|
Typical Composition (Weight %) | 0.32 | 0.70 | 1.60 | < 0.025 | < 0.010 | 1.40 | 1.50 | 0.60 | 0.004 |
Hardox 400 is a hardened fine-grain steel. Hardox 400 round bars are the new generation of wear-resistant round bars with a unique combination of high hardness, exceptional toughness, good bendability, and excellent weldability. This material is quenched and tempered using state-of-the-art processes and is ready for immediate use. The round bars are supplied in various diameters with a rolled surface from stock, peeled execution in tight tolerances is available upon request.
Hardox 400 round steel is available in diameters ranging from 13 to 100 mm and has the same guaranteed properties as the wear plate. Hardox 400 round steel is quenched and tempered to high tensile strength and hardness, offering completely new possibilities for a stronger and lighter construction.
Material Properties
Hardox 400 | Properties* |
---|---|
Hardness (HBW) | 400 |
Charpy V-notch Impact Toughness (J) | 65 (at -40°C) |
Yield Strength (MPa) | 1,000 |
Tensile Strength (MPa) | 1,350 |
Max. Carbon Equivalent (CET) | 0.37 |
Elongation at Break (%) | 13 |
* The data in this table represents typical values
Hardox 400 round bars are unique in their combination of mechanical properties, uniform hardness, and toughness to achieve the highest possible wear resistance. The properties that have led to the leading position of Hardox plates have been transferred to Hardox 400 round bars, especially in terms of wear resistance and weldability.
Mechanical Properties
Diameter (mm) | Hardness 1) (HBW) | Typical Yield Strength (MPa) |
---|---|---|
13.0 - 100.0 | 370 - 430 | 1,000 - 1,100 |
1) The hardness (HBW) is measured according to EN ISO 6506-1 on a machined surface in the sample position for Charpy impact test and tensile test (EN10083).
Hardox 400 is through-hardened. The minimum core hardness is 90% of the guaranteed minimum surface hardness.
Impact Toughness
Grade | Longitudinal Samples, Typical Impact Toughness, Charpy V-notch 10 x 10mm test specimen |
Longitudinal Samples, Guaranteed Impact Toughness, Charpy V-notch 10 x 10mm test specimen |
---|---|---|
Hardox 400 Round Bars | 45J / -40°C | Min. 27J / -40°C |
Carbon Equivalent CET (CEV)
Diameter (mm) | 40.0 - 100.0 |
---|---|
Max. CET (CEV) | 0.39 (0.60) |
Typ. CET (CEV) | 0.37 (0.58) |


Tolerances
Geometric Parameter | Description | DIN EN Standard |
---|---|---|
Diameter (rolled bars) | OD ≤ 75mm | DIN EN 10060 |
OD > 75mm | SSAB Specification | |
Diameter (peeled bars) | Possible to achieve h11, h9, h6, or f8 | EN 10278 |
Length | L = 5,000mm with -0/+200mm | DIN EN 10060 |
Ovality | < 75% of the diameter tolerance range | DIN EN 10060 |
Straightness | 2mm/m | DIN EN 10060 |
Surface
Black scale. Peeled surface available on request.
Processing and Other Recommendations
Hardox 400 is not intended for further heat treatment. Its mechanical properties are achieved through hardening and, if required, subsequent tempering already at the factory. The properties in the delivery condition cannot be maintained if the steel is exposed to temperatures above 250°C.
Machining Guidelines
Welding
Additional notes to the standard recommendations:
- Diameter is equal to the thickness of the plate.
- Increased preheating temperature for 40 to 50 mm to 175 °C.
- For other diameters, follow the same recommendations as for plates.

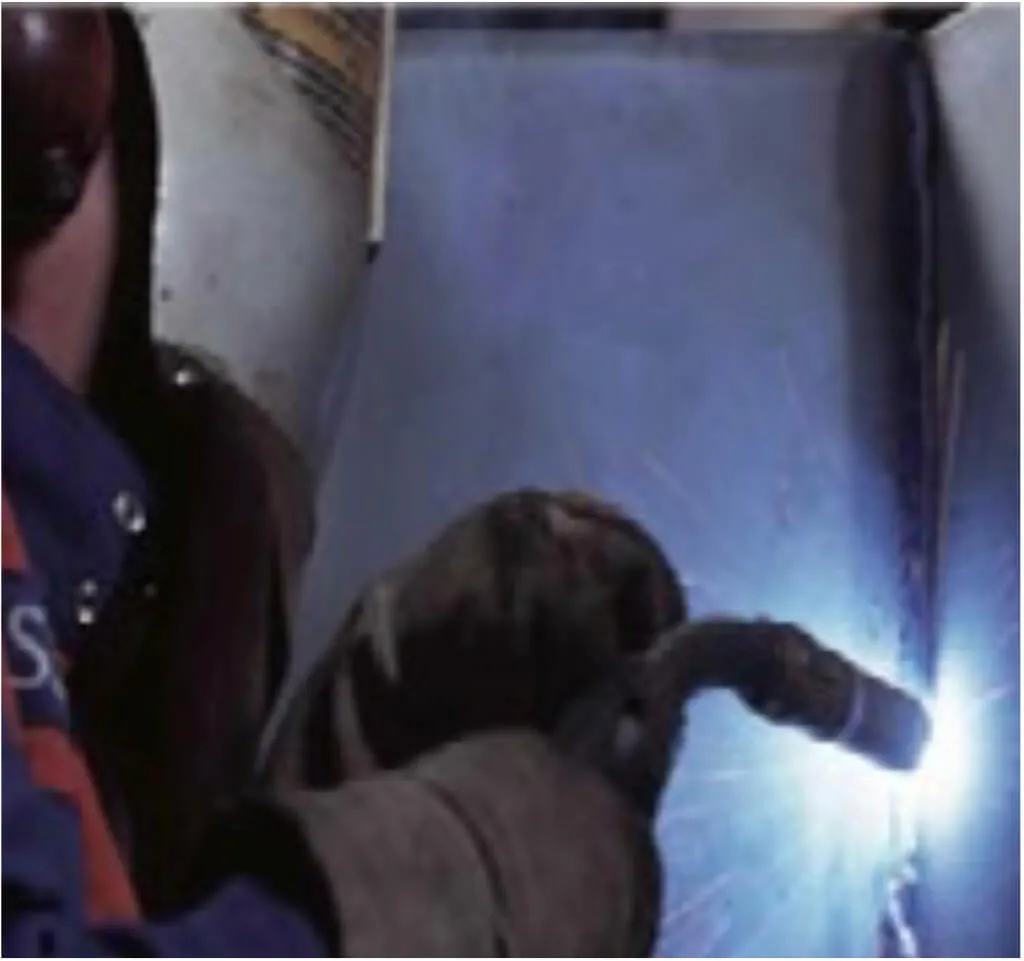
WeldCalc for Hardox 400 Round Bars
For diameters 40 to 50 mm, calculate the preheating temperature using the CET method. Do not use the plate recommendations from SSAB for 40 to 50 mm.
For diameters 50 to 100 mm, all features of WeldCalc can be used; i.e., preheating can also be used if these SSAB recommendations were chosen. Other features of WeldCalc can be used for all diameters of Hardox 400 round bars.
Bending
Additional notes to the normal recommendations
- Bare round bars (turned, peeled, ground) R/t 1.0.
- Hot-rolled R/t 1.5.
R = Radius, t = Diameter of the round bar
The minimum bending radius is smaller compared to the recommendations for sheets due to the shape. Our experience is based on normal bending tools.
The bending tools must always be as hard or harder than the round bar being bent to avoid excessive damage to the tool. High contact pressure between the tool and round bar can cause damage to the tool and the inner radius of the round bar. To minimize the high contact pressure, the tools must be profiled to match the dimensions of the round bar being bent.
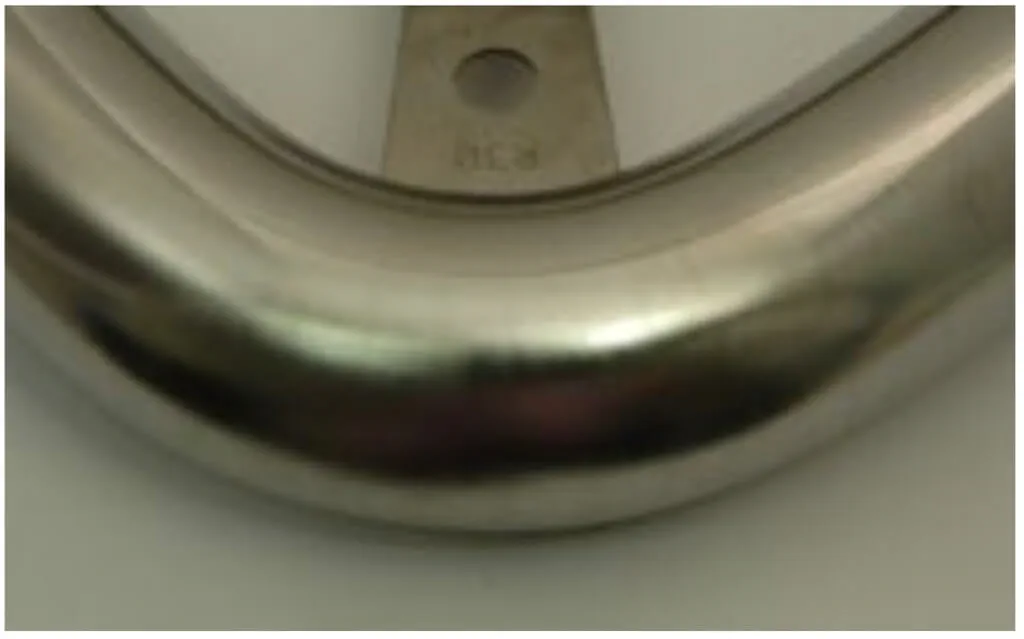
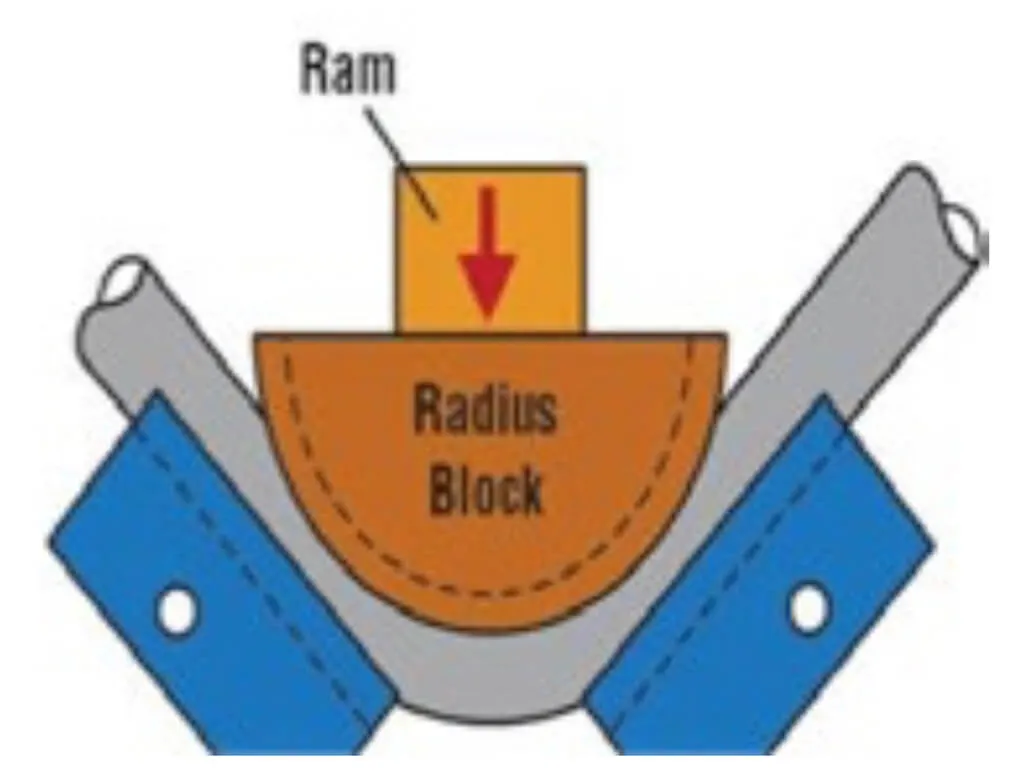
Drehen
Cutting Data Turning |
Carbide | |
---|---|---|
Roughing | Finishing | |
Cutting Speed, Vc (m/min) | 70 - 90 | 70 - 130 |
Feed per Revolution, fn (mm/U) | 0.2 - 0.6 | 0.05 - 0.3 |
Cutting Depth, ap (mm) | 2 - 4 | 0.5 - 2 |
Suitable Grades | P20 - P35* K20 - K30* |
K01 - K20* |
* If possible, use a CVD-coated carbide tool.
Note
These cutting values should be considered as initial values. The optimization of
cutting values for each machine is the responsibility of the workshop.
Remarks
- It is recommended to use coolant during turning. Internal coolant supply is advantageous.
- Use a tougher grade of carbide tool for interrupted cuts or facing large workpieces.
- If increased wear occurs, reduce the cutting speed.
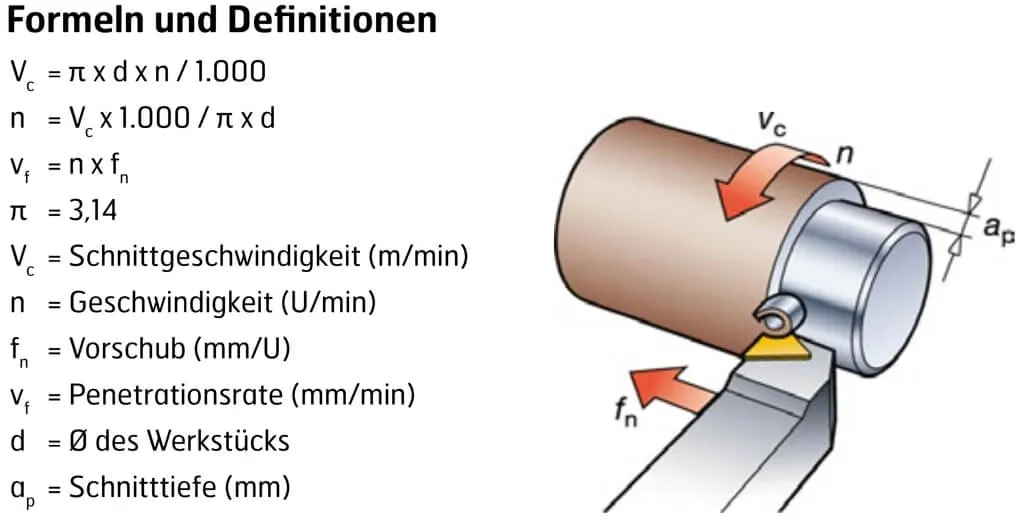
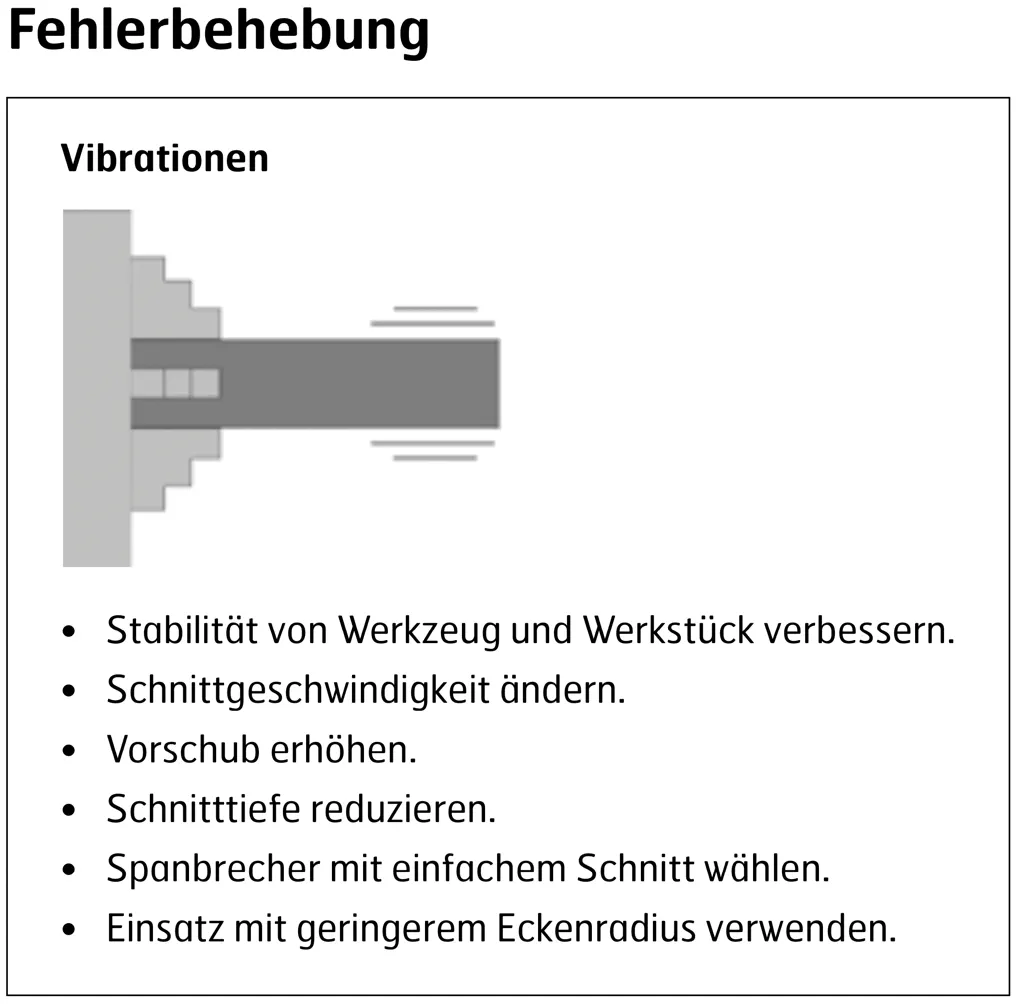
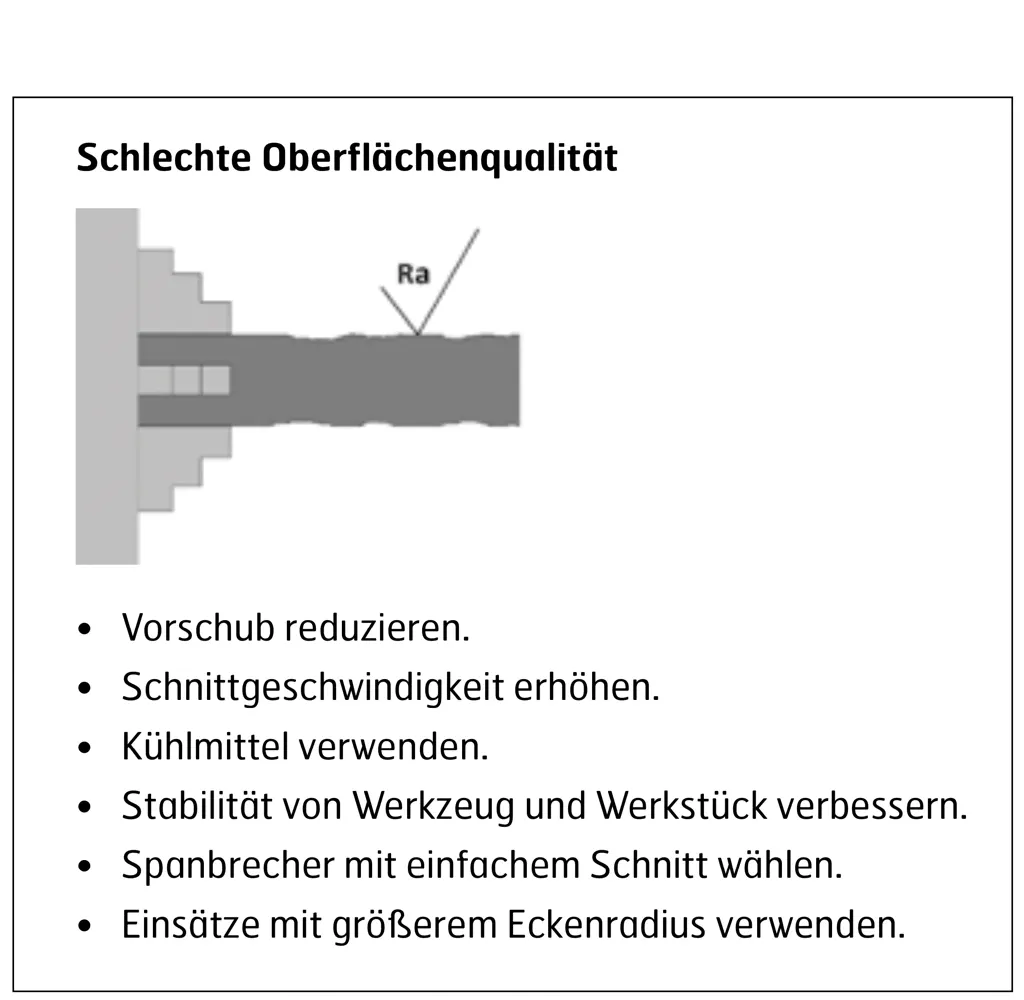
Sägen
Practical Tips
Teeth per Inch (TPI) indicates the size or spacing of the teeth and varies between 1 and 24. Large, solid workpieces with long engagement require a blade with fewer teeth per inch to allow more space for chip removal.
- It is essential that each tooth of the saw blade cuts with the correct depth of cut. Start by selecting a bandsaw blade with the appropriate pitch for the workpiece. (Consult the saw blade supplier for guidance.)
- Then, choose the correct band speed using the recommendations in the data sheet. Determine the correct feed rate by observing the chips generated by the bandsaw during cutting.
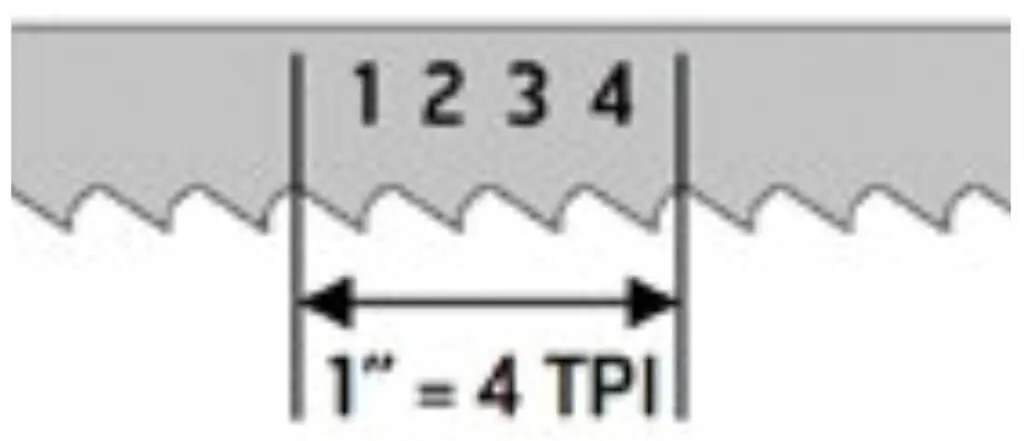
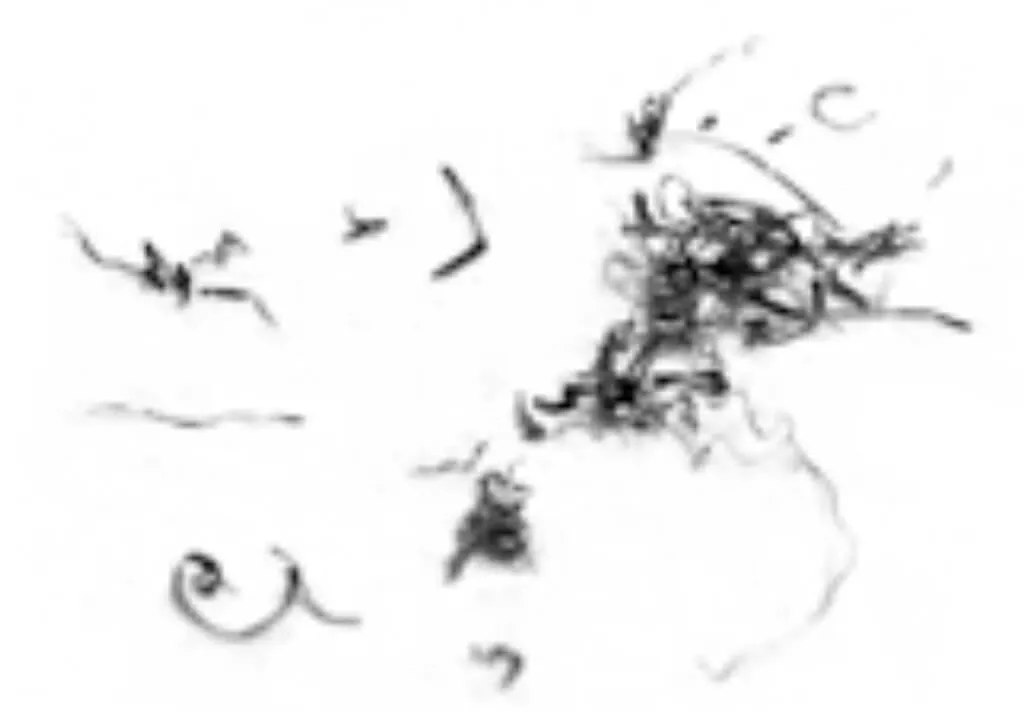
Thin or ground chips.
incrase feed rate
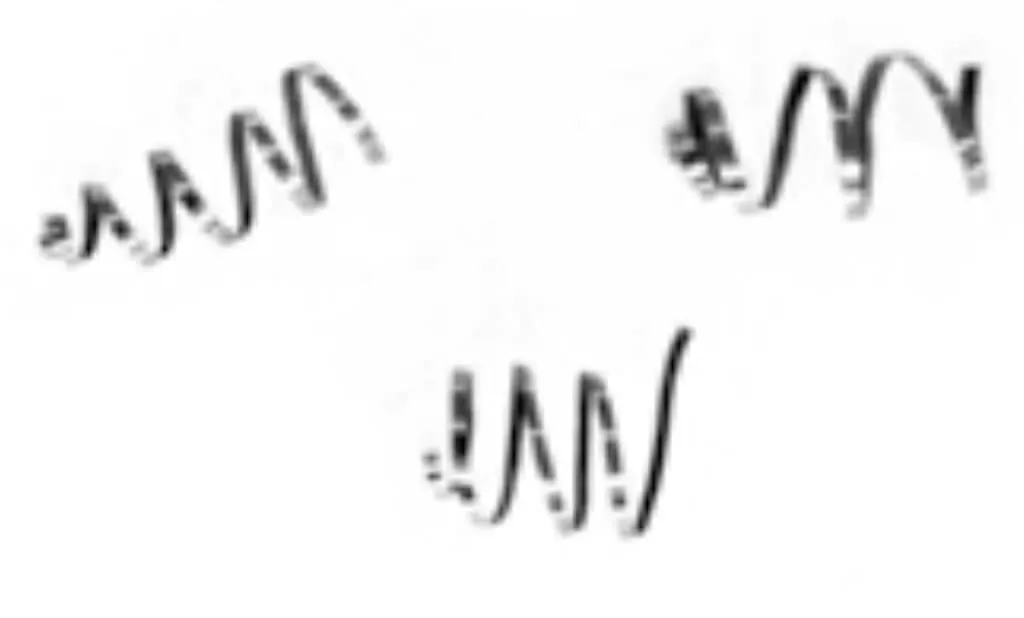
Lightly wavy chips.
Optimal feed rate
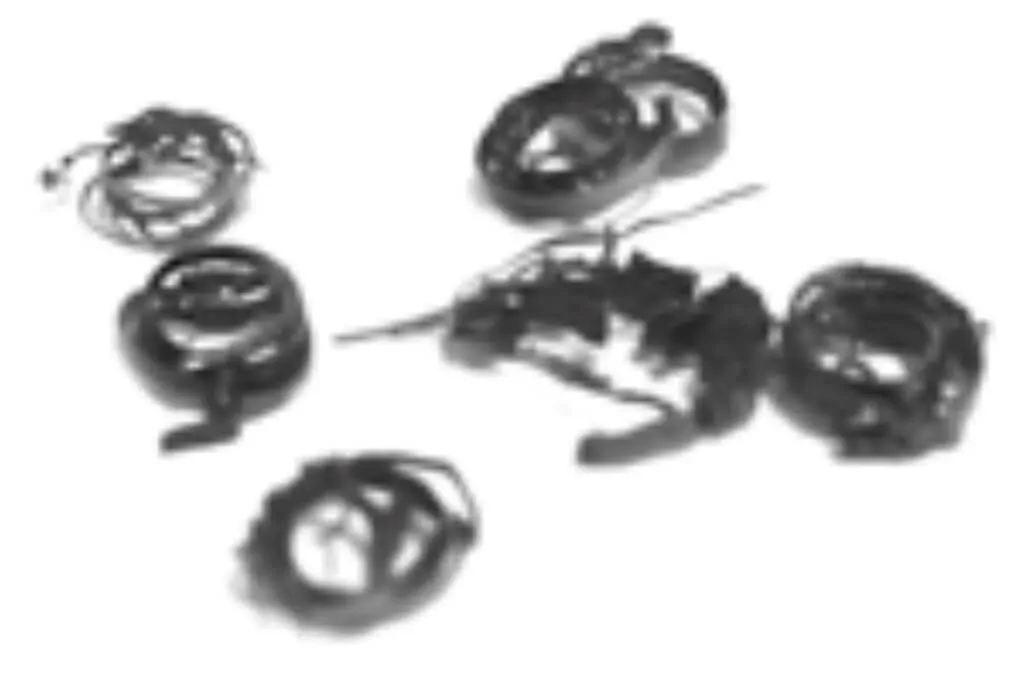
Thick, rough, or burnt chips.
Reduce feed/speed.
Band Speed (m/min) | ||||||
---|---|---|---|---|---|---|
Material | Bimetal Blade | Carbide Tipped Blade | ||||
Diameter >> | < 100 mm | 100 - 400 mm | > 400 mm | < 100 mm | 100 - 400 mm | > 400 mm |
30-35 m/min | 20-25 m/min | 15-20 m/min | 50-60 m/min | 40-50 m/min | 30-40 m/min |
Blade Break-In
A new bandsaw blade has very sharp tooth tips. To withstand the cutting pressures used in bandsaws, the
tooth tips must be ground to form a micro-fine radius.
How to Break-In a Bandsaw Blade?
Choose the correct band speed, see the table above. Reduce the feed force to achieve a feed rate of 30% to
50% of the normal rate in the first 10 minutes. In the following 10 minutes, gradually increase the feed rate to
the normal rate.
Coolant
Coolant concentrate with 8 - 10% mixture.
Please make sure to use a bandsaw blade suitable for Hardox and contact your tool supplier for that. As some experimentation and the right machine may be necessary, why not use our service? We are happy to cut your workpieces to the specified length according to your needs. For this purpose, we have HM-tipped bandsaws perfectly suited for the task. Simply calculate and order under VarioRond!
Maintenance
Band Wheels | Thoroughly remove chips. Ensure they rotate freely. |
Blade Tension | Use a measuring device to achieve accuracy. |
Blade Guides | Check that the blade runs correctly and is properly seated in the guides. |
Chip Brush | Securely install to prevent chip recutting. |
Guides | Ensure guides are not splintered or torn. The guides must hold the blade with the correct pressure and as close to the workpiece as possible. |
Guide Arm | Bring as close to the workpiece as possible for maximum support. |
Workpiece | Check that the workpiece is firmly clamped to prevent vibration during cutting. |
Protective Cover | Keep the protective cover on the blade until it is inserted into the machine to avoid damaging the tooth tips. |
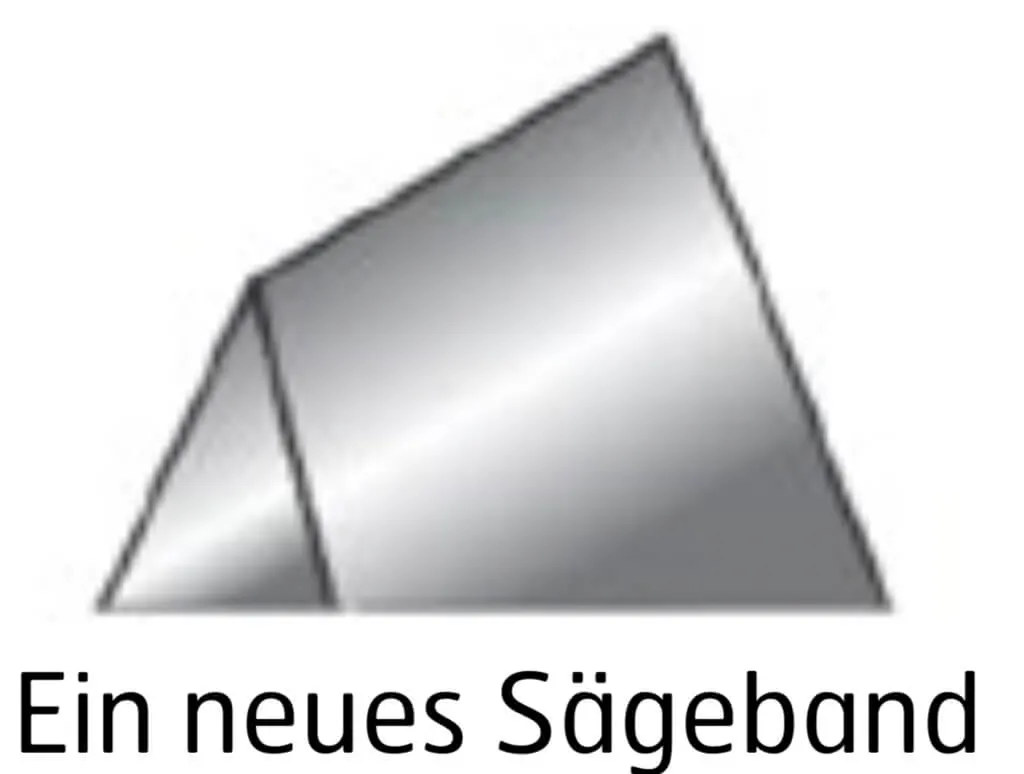
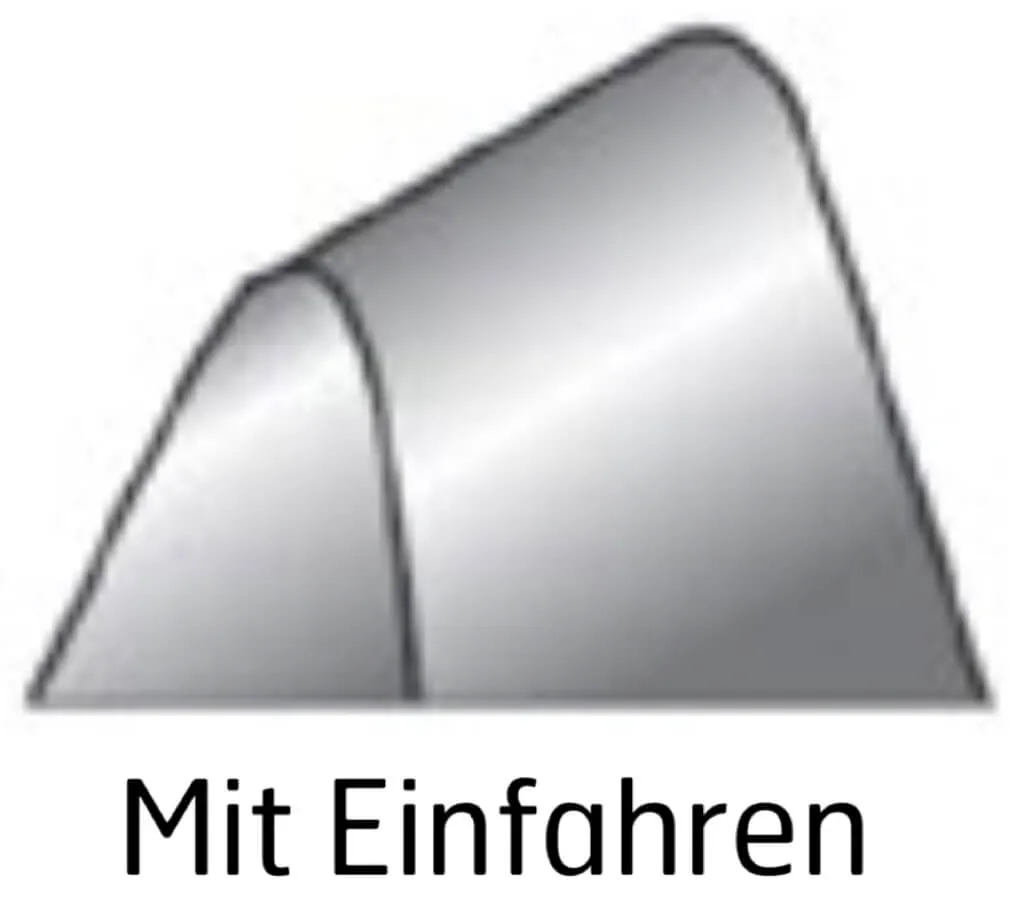
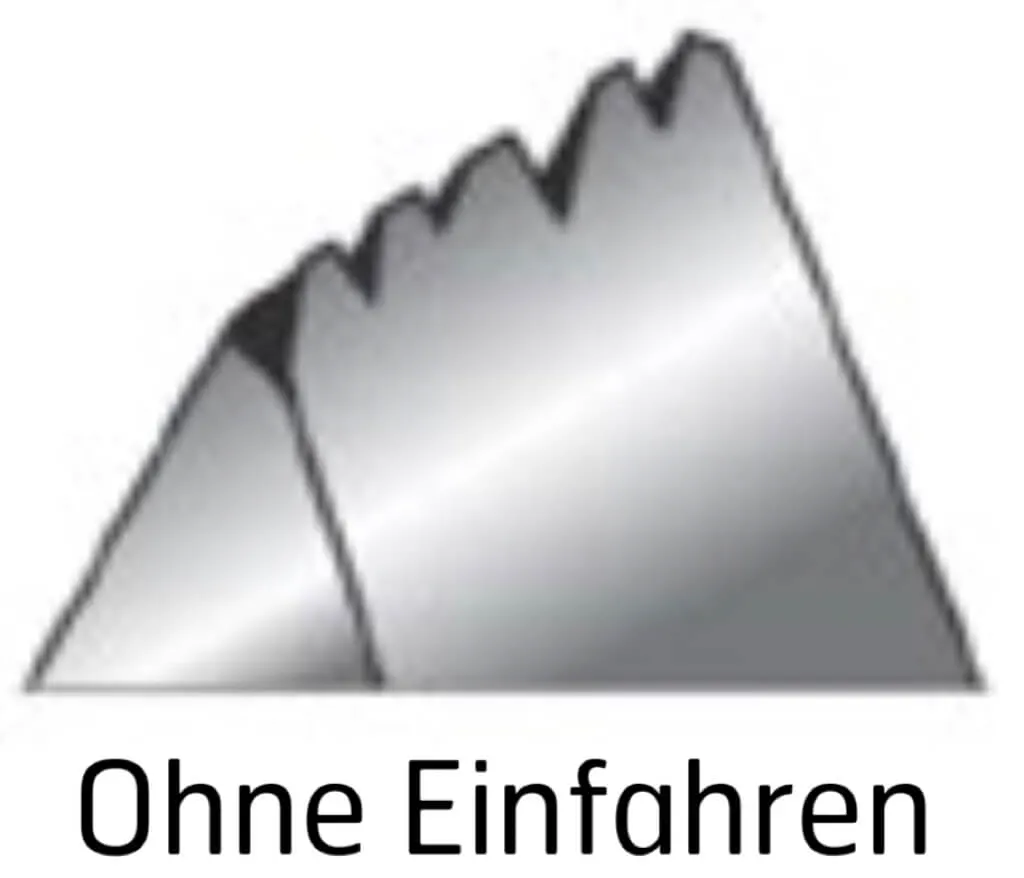
Attention please!
Some features of our webshop are not supported by your current browser version.
We recommend updating your browser or using a different browser.