Steel Glossary
Daido DCMX
C | Si | Mn | Cr | Mo | V | |
---|---|---|---|---|---|---|
Typical Composition (Weight %) | 0.7 | 2.0 | 1.0 | 6.8 | 1.4 | 0.2 |
Tempering
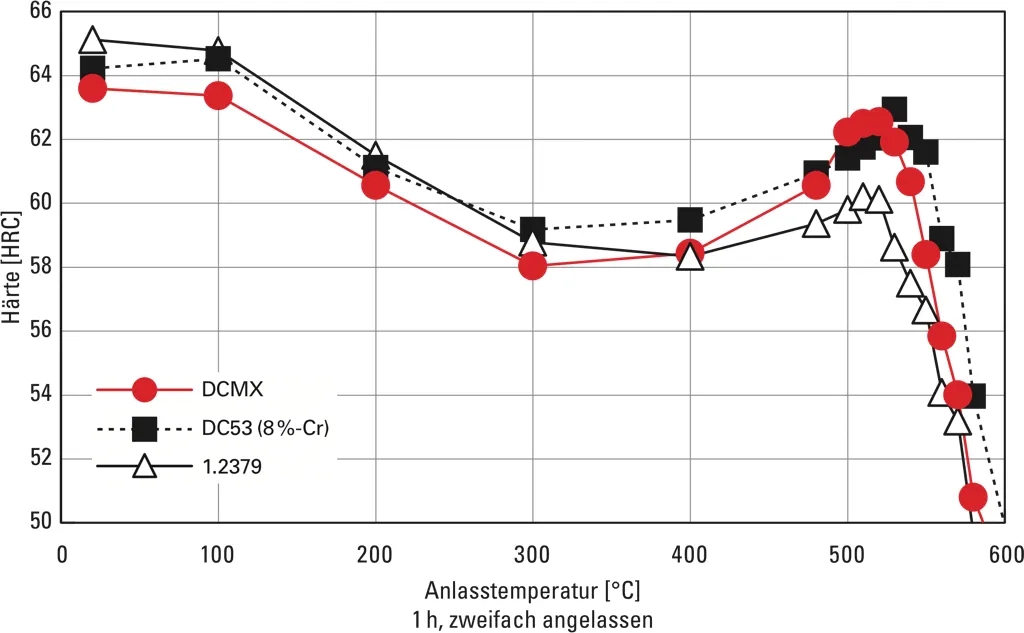
Sample: 15 mm, cubic
Hardening at 1,030°C, gas quenching
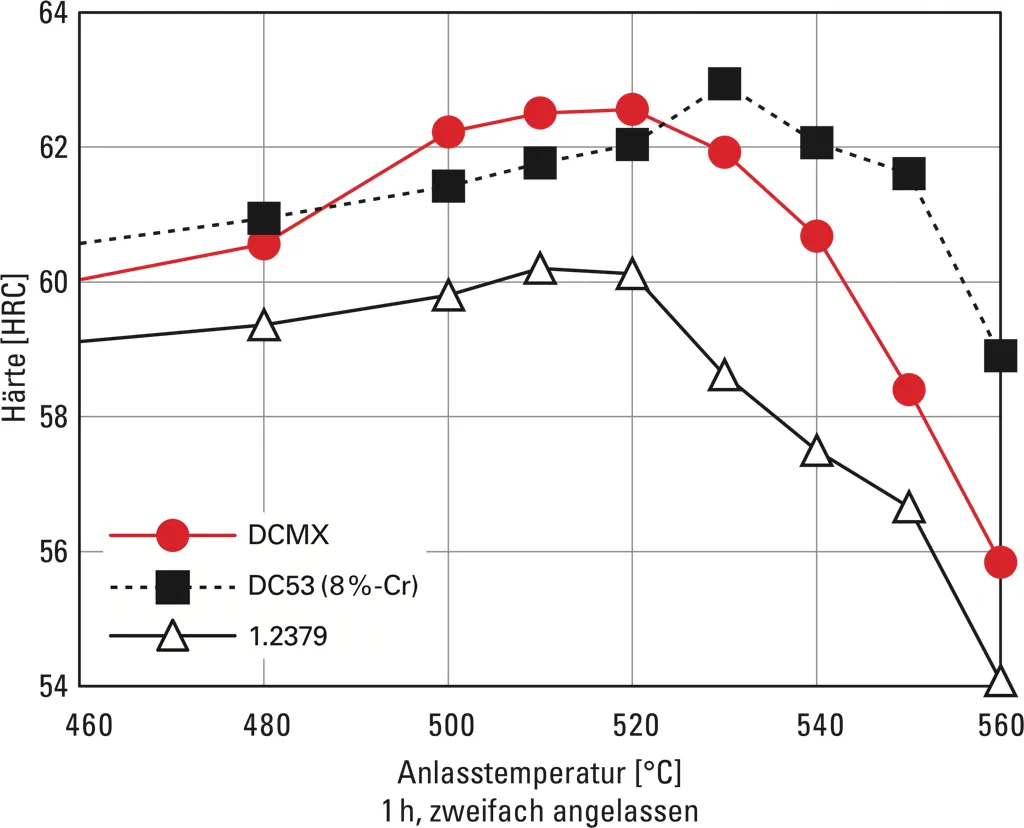
High-strength steels are increasingly used in automobiles to reduce weight. This leads to specific requirements for tool steels in terms of resistance to chipping, cracking, abrasive and frictional wear. Cost efficiency and secure manufacturing processes for the tools are essential. An optimized balance between hardness, toughness, and good machinability is of particular importance. So far, the dimensional stability and predictability during heat treatment and continuous operation have been challenging. The newly developed matrix cold work tool steel, DCMX, from our technology partner Daido in Japan, shows exceptional potential in addressing these issues.
Heat Treatment
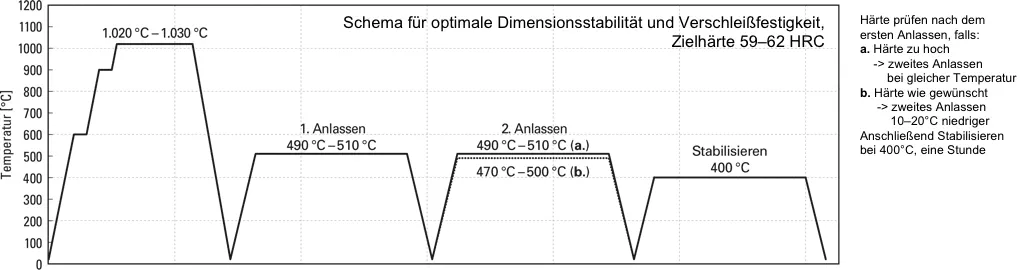
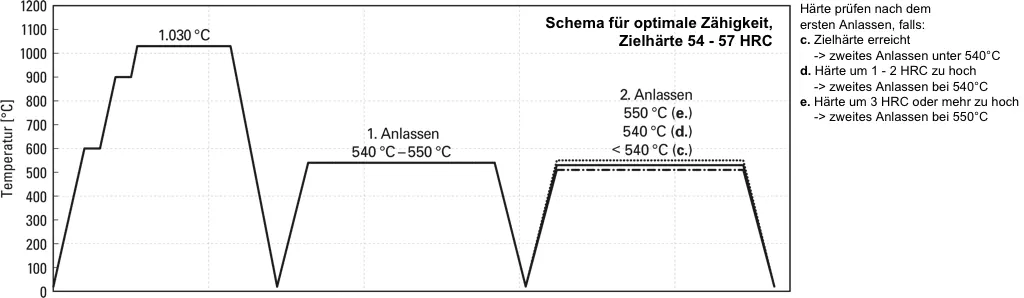
Treatment Temperatures | Hardness | |||||
---|---|---|---|---|---|---|
Warm forming (Hot forming) | Annealing | Hardening | Tempering | Stabilization | Annealed | Hardened |
900 – 1,160°C | 920 - 980°C Slow Furnace Cooling |
1,000 – 1,050°C Cooling In Air Or Gas |
Low: 150 – 200°C High: 480 – 560°C at least 2 times |
400°C für at least 1h | ≤ 235 HB | 56 – 62 HRC |
Microstructure
Daido DCMX exhibits a particularly fine microstructure, virtually free from coarse primary carbides.

Conventional steels often exhibit elongated primary carbides, and the difference in volume change during hardening in the longitudinal and transverse directions is caused by this, with higher carbide content exacerbating the effect. DCMX was developed to address this problem by significantly reducing the presence of primary carbides. In other words, it is a matrix cold work tool steel that shows minimal large primary carbides. As a result, it not only provides optimal dimensional stability but also significantly improves toughness and machinability.
Nowadays, larger punching and bending tools are segmented to counteract the well-known issue of dimensional changes during hardening. Common steels like 1.2379 / X 153 CrMoV 12 and even previously known 8%-Cr tool steels exhibit anisotropic behavior in the three spatial directions during hardening. This necessitates elaborate post-processing and division of functional parts into smaller segments.
The smallest difference in terms of dimensional changes in the spatial directions occurs at the highest hardness of 62 HRC after tempering at 500°C. Dimensional changes over time are a well-known phenomenon at high tempering temperatures. A stabilization treatment at 400°C after tempering effectively mitigates this issue.
Shape And Dimensional Stability (Isotropic Behavior)
Hardening: In An Open Atmosphere, 1030°C, Oil Quenching
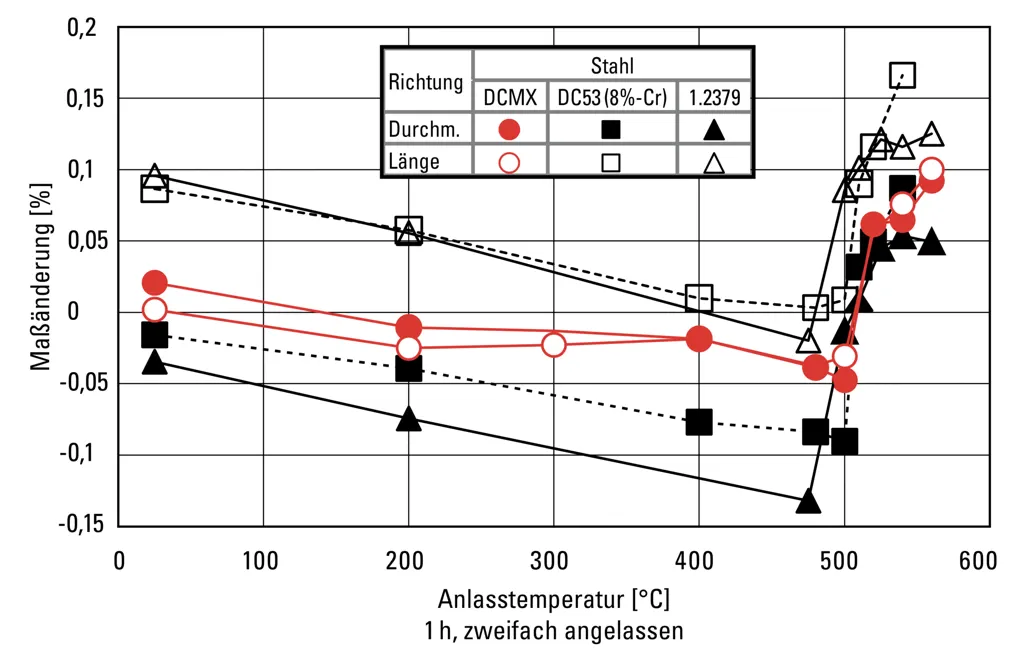
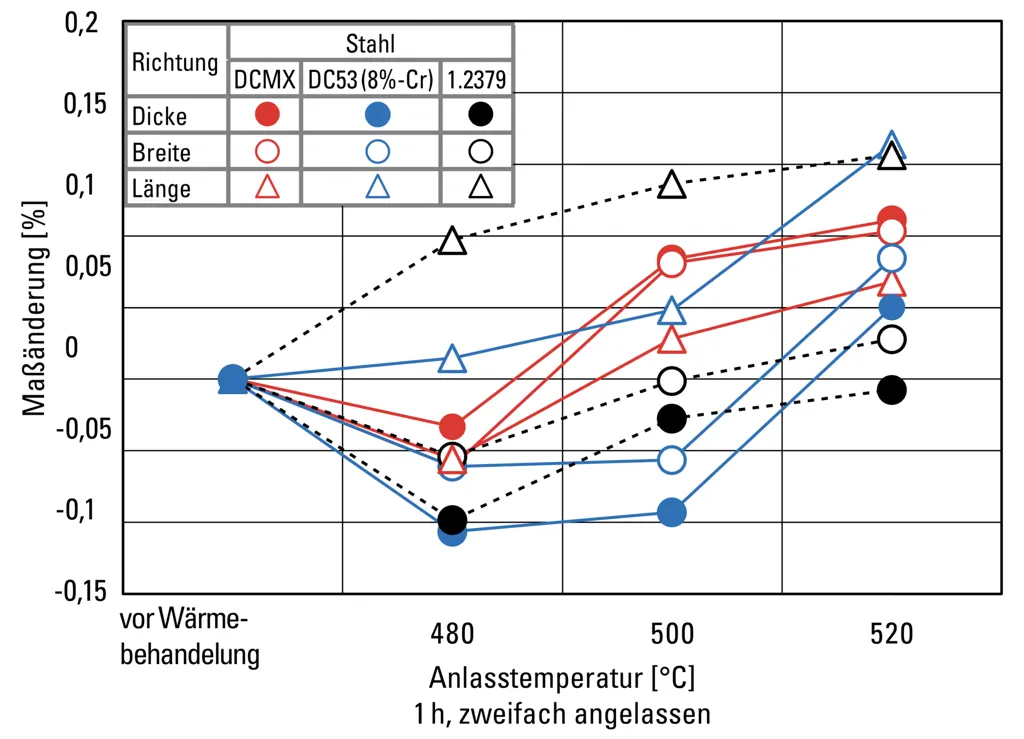
DCMX exhibits high toughness, not only compared to 1.2379 / X 153 CrMoV 12 but also when compared to 8%-Cr steels such as DC53 or TENASTEEL. This results in significantly reduced susceptibility to chipping or cracking. Additionally, its fatigue strength properties are outstanding.
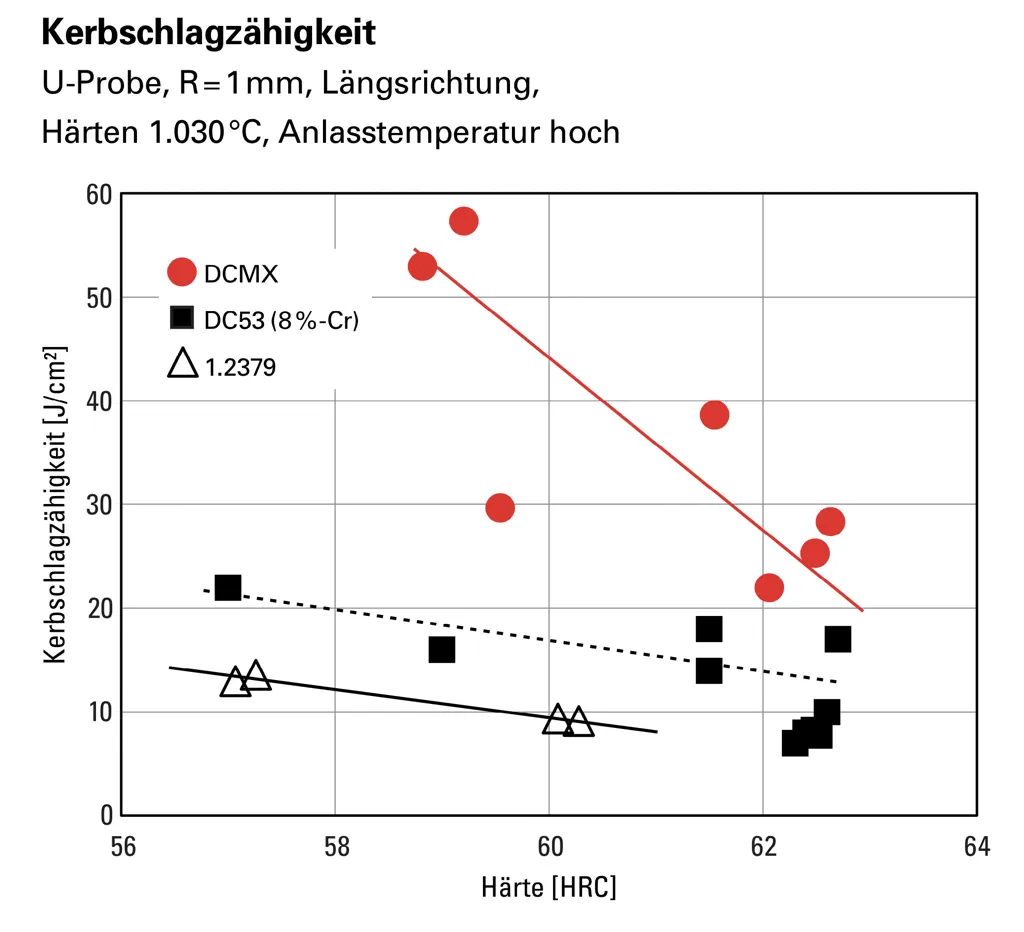
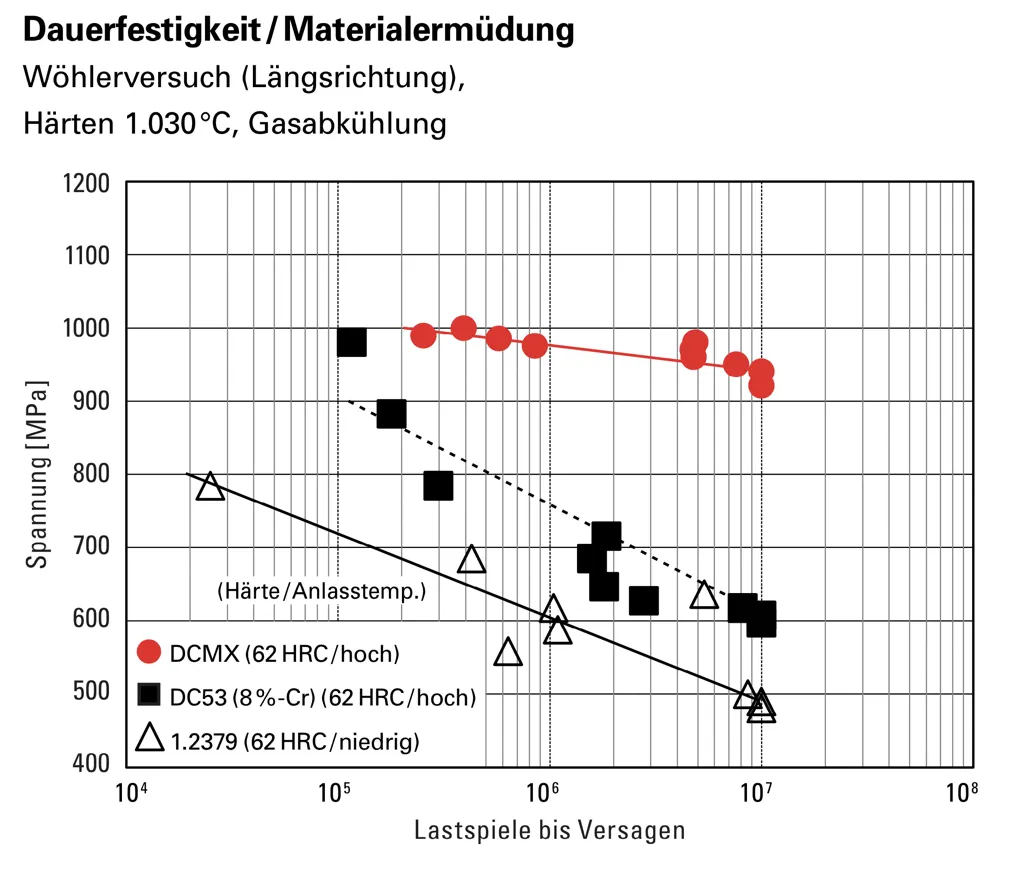
Both in the unhardened state and, particularly, in the hardened state, the machinability is exceptionally good, leading to longer tool life or the possibility of faster machining.
Comparative Machinability (in annealed state)
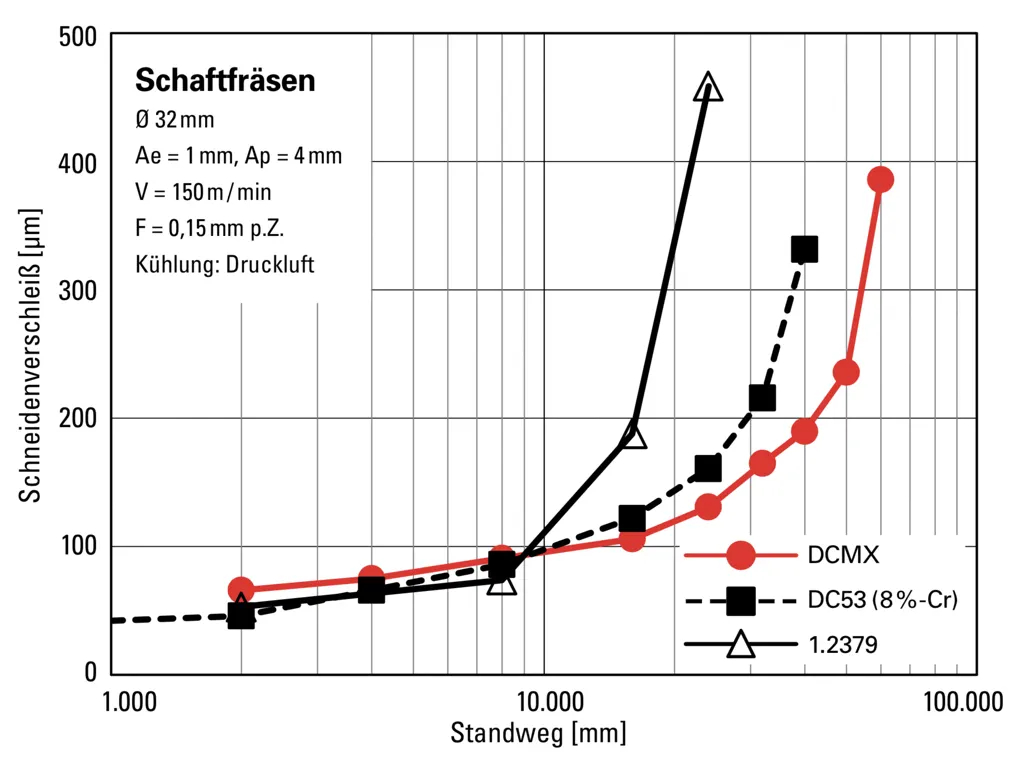
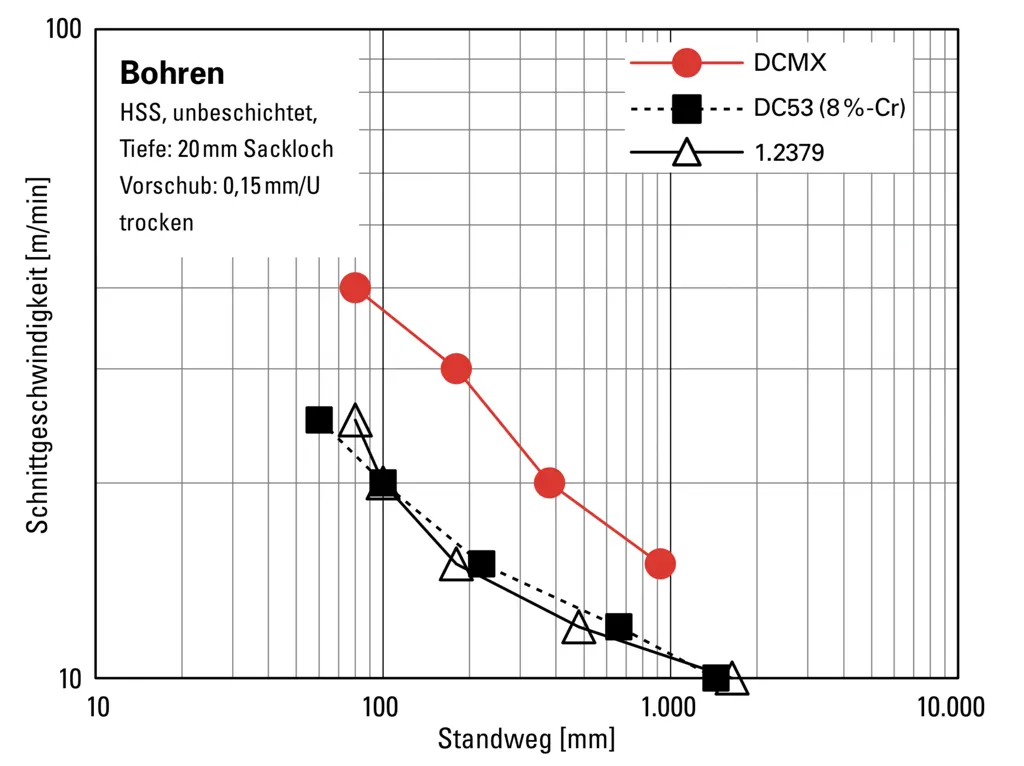
Wear Resistance (Pin-Disk Test)
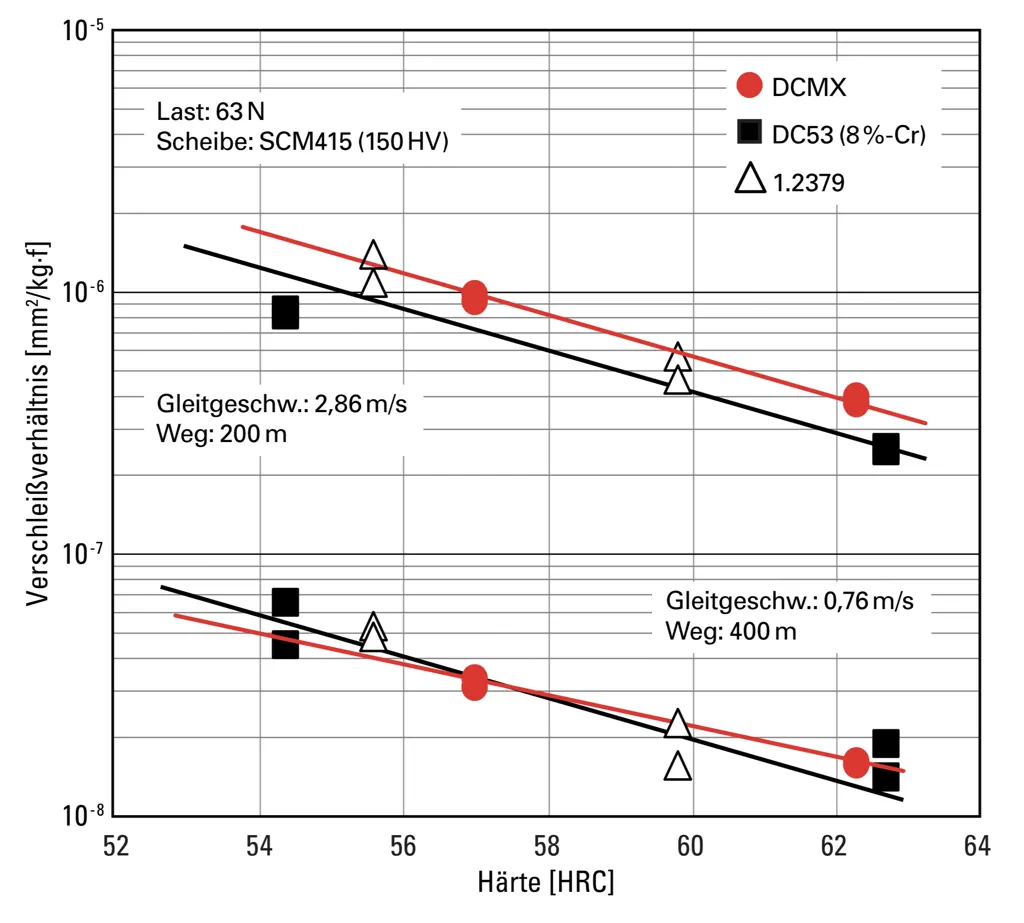
Wear resistance is a crucial criterion for steel selection. It is essential to distinguish between different wear mechanisms to make an appropriate choice. Adhesive wear, as occurs in bending and deep-drawing operations, can be assessed using the pin-disk test. It is evident that hardness is decisive for the wear behavior, and even at 62 HRC, DCMX demonstrates excellent toughness, setting it apart significantly from conventional materials. Abrasive wear can be evaluated using the friction wheel-sand test. Although DCMX, with its very fine carbide distribution, lacks coarse primary carbides, it still performs admirably in comparison. Both test methods demonstrate that DCMX is an optimally balanced material for improving tool life.
Coating
Thermoreactive diffusion layer: DOWA Thermo Engineering.
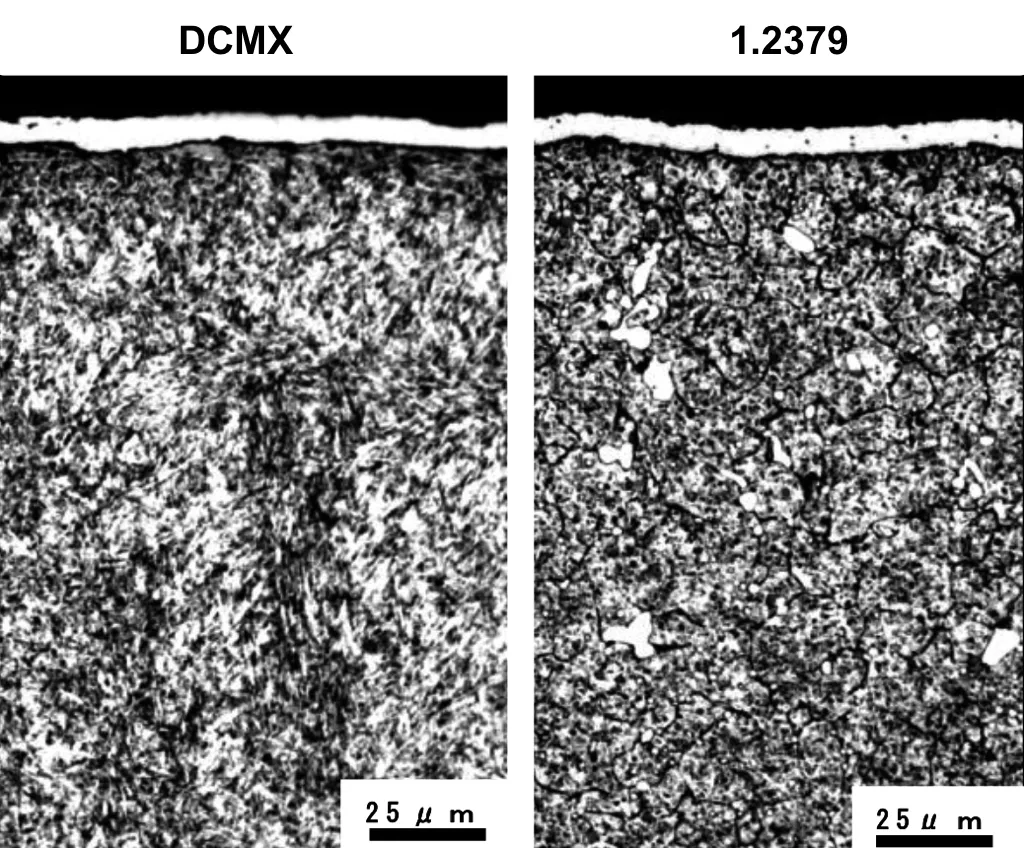
In Japan, more and more punching and bending tools are being PVD-coated to optimize tool life. DCMX is also excellently suited for this purpose. It provides very good adhesion, facilitated by its higher base hardness compared to 1.2379 / X 153 CrMoV 12.
Time-Temperature-Transformation Diagram
Hardening Temperature 1.030°C x 10min
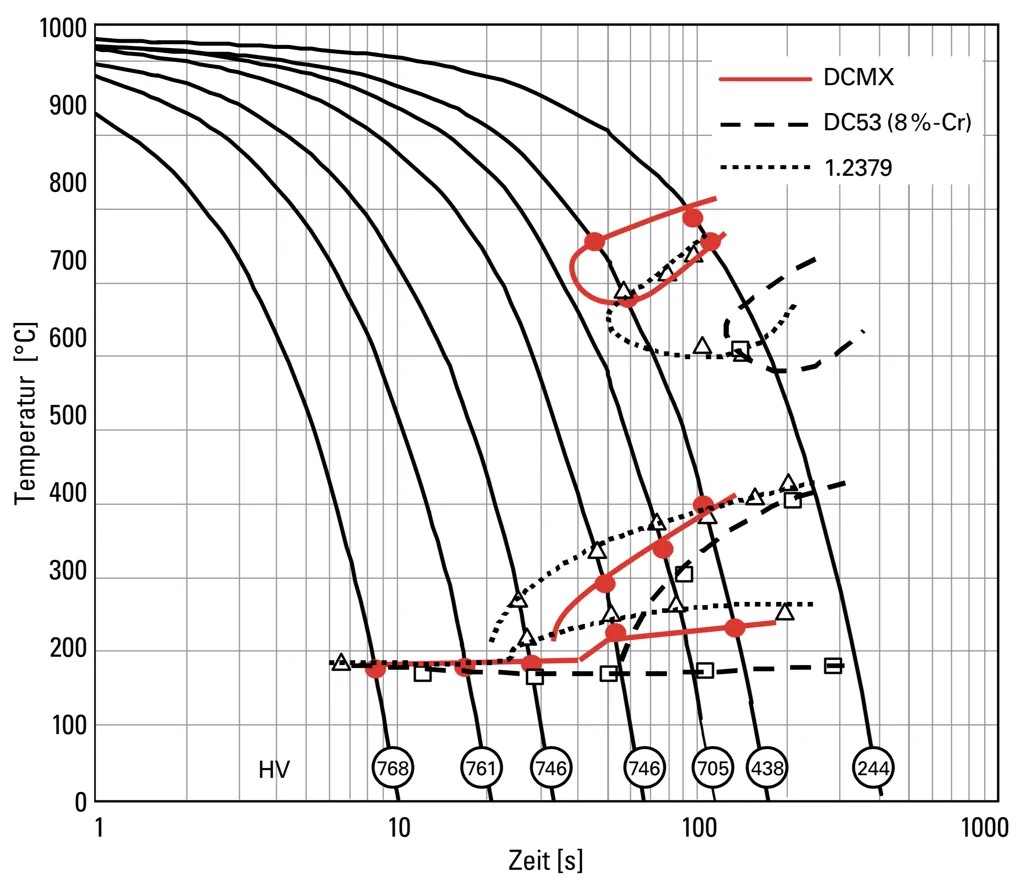
Physical Properties
Coefficient of Thermal Expansion [10-6/K] | ||||||
---|---|---|---|---|---|---|
20-100°C | 20-200°C | 20-300°C | 20-400°C | 20-500°C | 20-600°C | 20-700°C |
13.3 | 13.7 | 14.0 | 14.4 | 14.7 | 14.9 | 14.9 |
Thermal Conductivity [W/mK] | ||||||
---|---|---|---|---|---|---|
RT | 100°C | 200°C | 300°C | 400°C | 500°C | |
17.1 | 18.8 | 20.9 | 22.6 | 24.0 | 25.7 |
Specific Heat [J/kgK] | ||||||
---|---|---|---|---|---|---|
RT | 100°C | 200°C | 300°C | 400°C | 500°C | |
507 | 535 | 570 | 611 | 654 | 719 |
E-Modul = 202 GPa, Specific Gravity = 7,67 kg/dm³, Sample Hardened bei 1.030 °C, Air Cooled, 2 x Tempered at 500 °C
In certain cases, repair welding becomes necessary. For this purpose, DCMX offers comparatively good conditions. Preheating at 350°C and post-welding heat treatment at 400°C result in a uniform hardness distribution and provide resistance against welding cracks.
DCMX is also successfully used for larger automotive-type tools. Customers appreciate the predictability and reliability of dimensional stability, as well as the significantly longer tool life.
In summary, a matrix cold work steel that relies on reducing primary carbides combines three advantages: almost complete avoidance of problems due to dimensional changes during hardening, significantly improved machinability, and high toughness and fracture resistance.
(Summary translation of a technical article by Takayuki Shimizu, Koichiro Inoue, Atsushi Sekiya from Denki-Seiko (Electric Furnace Steel), Issue 81 (2010), No. 1, page 53 ff.)
Representative technical values based on our investigations are always provided. If not specified otherwise, they do not constitute guarantees. Please seek individual advice in specific cases.
Material Comparison
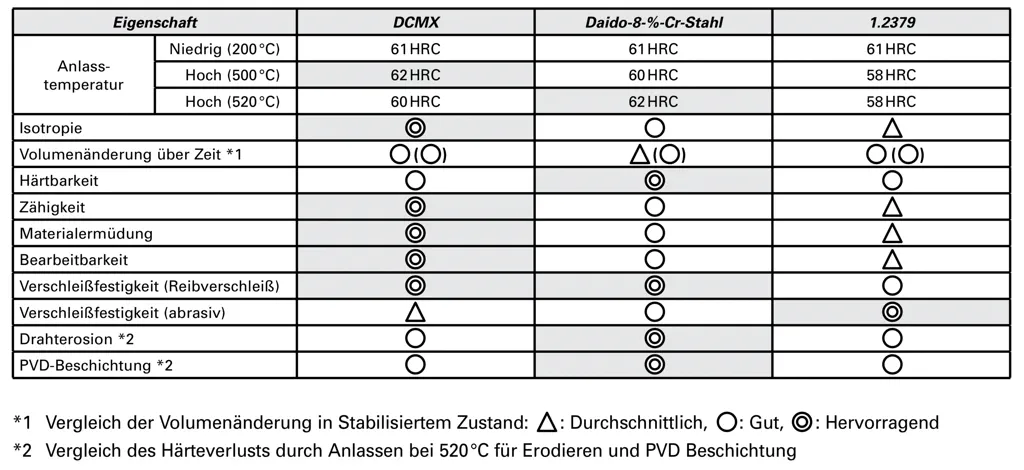
Attention please!
Some features of our webshop are not supported by your current browser version.
We recommend updating your browser or using a different browser.